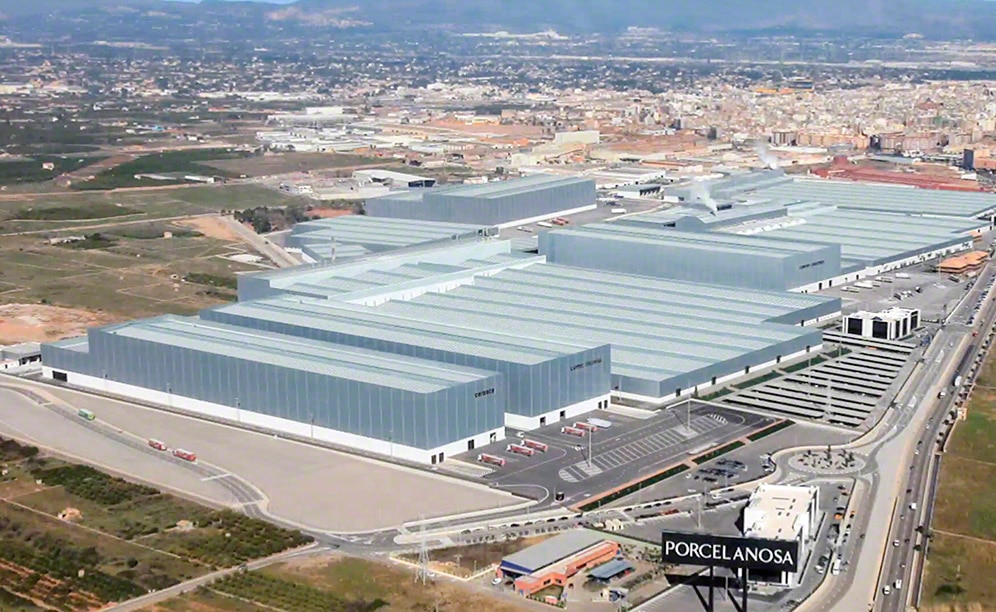
Porcelanosa Gruppo, leader mondiale del suo settore, ha introdotto le tecnologie più all'avanguardia in tutti i suoi processi logistici
Porcelanosa Gruppo e Mecalux: un lungo rapporto di fiducia, crescita e successo
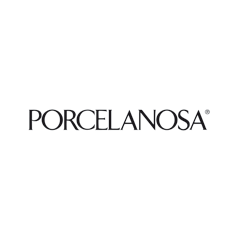
Il complesso logistico di Porcelanosa Gruppo a Vila-real (Spagna) è composto da cinque centri logistici con magazzini automatici di grande capacità. L’azienda, che spicca per la sua costante innovazione, ha introdotto l’ultima tecnologia in tutti i suoi processi logistici. Ciò le ha permesso di espandersi e rinforzare la sua leadership a livello internazionale. Mecalux ha creato e implementato le soluzioni di stoccaggio più efficienti e adatte alle esigenze di questa azienda. Allo scopo di affrontare l’evoluzione del mercato, i centri sono stati preparati per crescere ed ampliare la loro superficie di stoccaggio senza interrompere i cicli operativi.
A proposito di Porcelanosa Gruppo
Porcelanosa Gruppo è uno dei gruppi aziendali spagnoli più solidi e con maggior riconoscimento a livello mondiale. È stato fondato nel 1973 presso la cittadina di Vila-real (a soli 70 km da Valencia), con una chiara vocazione internazionale. Attualmente, vanta una presenza capillare in circa 150 paesi.
Inizialmente, Porcelanosa Gruppo si dedicava alla produzione di piastrelle, ma la diversificazione dei suoi prodotti e servizi è stata fondamentale per rafforzare la sua crescita. Oggi offre un’ampia gamma di pavimenti e rivestimenti in ceramica e naturali, facciate a doppia pelle, mobili da cucina, sanitari, rubinetteria e soluzioni edilizie per l’architettura contemporanea.
Il gruppo è formato da otto aziende: Porcelanosa, Venis, Gamadecor, Systempool, L’Antic Colonial, Butech, Noken e Urbatek.
Cinque magazzini automatici
I centri logistici che la società possiede a Vila-real si trovano in una posizione idonea per distribuire tutti i suoi prodotti in modo rapido sia in Spagna che nel mondo.
Nel 2003, Mecalux ha costruito il primo magazzino automatico di Porcelanosa Gruppo. Tenendo conto dei requisiti presentati, delle previsioni di crescita e della strategia aziendale della compagnia, venne valutata la possibilità di costruire un magazzino diverso per Porcelanosa, Venis, L’Antic Colonial, Noken e Urbatek. Questo progetto di grandi dimensioni si estese per un periodo di 10 anni.
Il team tecnico di Mecalux ha lavorato insieme a quello di Porcelanosa Gruppo allo scopo di progettare la soluzione migliore per risolvere le sue esigenze logistiche. Il risultato è un modello di magazzino automatico che è valido per ognuna delle aziende (adattato alle varie dimensioni, ai volumi e alla rotazione dei diversi prodotti).
La progettazione spicca per la sua semplicità: il magazzino è composto da trasloelevatori che effettuano automaticamente l’entrata e l’uscita merci, mentre il ricevimento, la spedizione e il picking vengono finalizzati in testata con l'ausilio di un circuito completo di rulliere e navette.
Con questo tipo di soluzione, Porcelanosa Gruppo ha potuto raggiungere il rendimento desiderato in ognuno dei suoi centri, così come fornire un servizio agile ed efficiente. In pratica, l’unica differenza tra loro è la capacità di stoccaggio dato che il ciclo operativo è molto simile.
Mecalux e Porcelanosa Gruppo
Le due aziende hanno stabilito una stretta partnership fin dagli anni '80. Infatti, la storia di Porcelanosa Gruppo e quella di Mecalux hanno seguito una traiettoria molto simile: le due imprese basano la loro crescita sullo sviluppo tecnologico e vantano un’ampia rete di distribuzione internazionale.
Mecalux ha attrezzato i magazzini regionali di Porcelanosa Gruppo e i suoi centri di distribuzione, sia in Europa che nel continente americano.
I primi magazzini non avevano né il grado di automazione né di sofisticazione che attualmente hanno raggiunto. Si trovavano in edifici meno alti e gli operatori utilizzavano mezzi di sollevamento con uomo a bordo per movimentare i pallet. Inoltre, la preparazione degli ordini veniva effettuata secondo il criterio “uomo verso prodotto”.
Tuttavia, la forte crescita che viveva l’azienda in Spagna si tradusse nella necessità di costruire altri magazzini, sempre più alti e con un’ampia capacità. Per ottenere un maggior rendimento, era necessario fare un passo avanti verso l’informatizzazione della gestione e, successivamente, verso l'automazione di tutti i cicli operativi.
Centri logistici di Vila-real
I centri logistici di Porcelanosa Gruppo si trovano su una vasta area. Coprire queste grandi distanze poteva comportare un elevato costo di movimentazione all’ora per il trasferimento della merce, un aspetto che era necessario ottimizzare.
La proposta fu quindi che ognuno dei magazzini fosse il più vicino possibile alle uscite dalla produzione. Inoltre, la comunicazione tra le due zone si realizzò attraverso tunnel con rulliere automatiche in modo da evitare la movimentazione permanente di carrelli elevatori convenzionali.
L’esecuzione dei diversi progetti si concluse in modo progressivo. Il primo magazzino fu quello di Porcelanosa, messo in funzione nel 2003; seguì quello di Urbatek nel 2007, quindi vennero costruiti i magazzini di L’Antic Colonial e Noken e, infine, quello di Venis nel 2011.
Un’alta percentuale del rifornimento dei magazzini di Urbatek e L’Antic Colonial proviene dall’esterno, per questo motivo la loro ubicazione è in uno degli estremi del centro logistico. Per quanto riguarda il magazzino di Noken, questo di trova in un edificio vicino alla sede principale, presso la cittadina stessa.
Dei cinque magazzini, quattro sono molto simili tra loro (magazzino automatico per pallet); solo quello di Noken (magazzino automatico per contenitori) si distingue dagli altri. Per poterne comprendere il funzionamento, di seguito vengono descritti tre dei cinque magazzini automatici di Porcelanosa Gruppo.
Il magazzino di Venis
Fondata nel 1986, Venis produce pavimenti e rivestimenti in ceramica con un’ampia varietà di forme, tipologie e finiture. Si contraddistingue per la versatilità del design e l’uso della tecnologia più avanzata per la produzione di piastrelle e gres porcellanato.
Il magazzino automatico è costruito all'interno di un edificio di 35 m di altezza e occupa una superficie totale di 25.000 m2. Cio-nonostante, sono stati occupati 8.000 m2 per lo stoccaggio, riservando lo spazio restante per un ampliamento futuro.
Questo magazzino è separato dall'impianto di produzione, per cui la comunicazione tra i due centri è automatica, attraverso un tunnel sotterraneo formato da rulliere ed elevatori.
Il magazzino è composto da dieci corsie di stoccaggio, con scaffalature a singola profondità sui due lati, in ognuna delle quali circola un trasloelevatore.
All’estremo delle corsie, vi sono due livelli di trasporto, in quello superiore si effettuano le entrate e in quello inferiore le uscite. Un totale di otto elevatori collegano i due livelli, ottenendo così il flusso di movimentazioni richiesto. Esiste un’entrata diretta per la merce proveniente dalla produzione e due entrate ausiliarie che introducono i pallet di altri centri così come i pallet vuoti. In tutti i casi, i pallet devono superare un rigoroso controllo qualità prima di entrare nel magazzino.
Il picking costituisce la fase operativa fondamentale di questo magazzino e ogni giorno si prepara un numero molto elevato di ordini. Per questo motivo, è stata adibita un’ampia zona di picking di fronte alle corsie di stoccaggio.
Entrata magazzino
L’impianto inizia con l’uscita delle linee di produzione. Le rulliere del tunnel sotterraneo trasportano la merce in modo automatico fino al magazzino.
Sia all’inizio che alle fine del tunnel, sono stati installati elevatori che portano i pallet fino al relativo livello. Una volta che i pallet arrivano in magazzino, due elevatori si occupano di sollevare la merce fino al piano superiore. Ciascuno di essi è in grado di trasportare due pallet con un peso massimo di 1.600 kg.
Gli elevatori dispongono di elementi di sicurezza come recinzioni, barriere ottiche, porte di accesso sicuro perla manutenzione e porte rapide automatiche per il passaggio dei pallet.
Nel piano superiore, è stato installato il circuito di rulliere di entrata al magazzino. È presente un circuito che consente la distribuzione dei pallet in tutta semplicità prima che si verifichino eventuali problemi. Allo stesso tempo, comunica con il resto degli elevatori che sollevano i pallet che provengono dall’area di picking e dalle entrate ausiliarie.
Le entrate ausiliarie sono situate su uno dei lati del magazzino e sono destinate ai prodotti provenienti dall’esterno e ai pallet vuoti che sono stati generati durante il picking. I pallet vuoti vengono impilati e introdotti nella compattatrice per garantire stabilità e dimensioni prima di entrare nel magazzino.
Caratteristiche del magazzino
Il magazzino è lungo 160 m e alto 31 m. È composto da dieci corsie con scaffalature bifronti con 23 livelli, con la possibilità di bifronti. In totale, la capacità di stoccaggio ottenuta è di 65.320 posti pallet da 800 x 1.200 mm, un’altezza massima di 1.450 mm e un peso ammissibile massimo di 1.600 kg.
I trasloelevatori bicolonna operano a una velocità di traslazione di 180 m/min, effettuando un totale di 237 cicli combinati all’ora. Con queste attrezzature si ottiene un flusso di movimentazioni molto elevato senza richiedere l'intervento degli operatori ed eliminando eventuali errori logistici causati dalla gestione manuale.
I trasloelevatori, attrezzati con un rigeneratore di energia, sono in grado di recuperare e restituire alla rete elettrica il 15% circa dell’energia generata durante le operazioni di discesa della culla e decelerazione dell’asse di traslazione.
Area di picking
È stata disposta nel piano terra, dietro il circuito di rulliere di uscita e di fronte alle corsie di stoccaggio. È formata da otto postazioni di picking allineate, dove vengono preparati in totale 32 ordini contemporaneamente.
Ogni postazione di picking dispone di un'area di accumulo dei pallet utilizzati nel ciclo operativo che saranno trasportati fino alle stazioni di picking nel momento richiesto. Congiuntamente, il circuito a reticolo permette di sistemare la merce nei pallet seguendo criteri di impilabilità.
Per agevolare le manovre degli operatori, ogni postazione è dotata di un braccio di movimentazione meccanico che solleva i pacchi più pesanti con il minimo sforzo.
D’altra parte, i tavoli di preparazione con i pallet di picking (dove si prelevano i prodotti che compongono ogni ordine) e quelli di consolidamento (dove vengono depositati gli articoli) vengono sollevati tramite un sistema idraulico per posizionare il pallet in una posizione ergonomica.
Inoltre, sono stati installati quattro elevatori che inviano i pallet con i prodotti rimanenti al piano superiore per entrare nuovamente in magazzino. Vi sono anche due navette doppie che gestiscono i pallet vuoti e gli ordini già terminati. Questi passano per la stazione di imballaggio e, infine, vengono distribuiti in due canali di precarico, prima della loro spedizione.
Un tunnel pedonale, che attraversa la parte inferiore delle corsie dove sono presenti le navette e le rulliere con le postazioni di picking, collega l’area di picking con il resto del magazzino.
Comunicazione
Separando le entrate dalle uscite in due piani, si evitano interferenze tra le due fasi operative. Le movimentazioni sono costanti: l’entrata e l'uscita di ogni corsia sono fluide.
È stata adibita un’ampia zona di precarico dove vengono preparati i pallet pronti per la spedizione. Le merci già sottoposte a consolidamento vengono accumulate in questa area, poi vengono trasferite sugli automezzi per il trasporto e la distribuzione.
Vi sono due blocchi di precarico (1 e 2) con sei canali dove accumulare i pallet. Questo sistema riduce notevolmente il tempo destinato al caricamento dei camion
Il magazzino di L’Antic Colonial
La varietà di prodotti disponibili ha generato esigenze specifiche in alcuni magazzini del gruppo. È il caso di L’Antic Colonial, azienda produttrice di rivestimenti per pavimenti e pareti che opera con pacchi piani di grandi dimensioni (parquet) su pallet da 2.440 x 1.200 mm.
Mecalux ha progettato su misura tutte le attrezzature di movimentazione per manipolare questi prodotti e collocarli correttamente sui livelli assegnati. I trasloelevatori, le rulliere, gli elevatori, le postazioni di picking e le navette sono doppi.
Oltre alle postazioni di picking con delle dimensioni consuete, è stata inoltre adibita una zona indipendente per preparare gli ordini che contengono prodotti di grandi dimensioni, situata perpendicolarmente rispetto alle corsie dove vengono stoccati. Le rulliere e la navetta collegano il magazzino con le postazioni di picking.
Il magazzino di Noken
Per quanto riguarda Noken, azienda specializzata nell’arredamento di sale da bagno, è stato costruito un magazzino automatico per contenitori miniload (anziché un magazzino per pallet) a causa delle piccole dimensioni e del peso ridotto dei suoi articoli, principalmente rubinetteria e accessori da bagno.
Il magazzino è composto da due corsie lunghe 70 m e scaffalature a singola profondità ai lati. Sono alte 15 m e hanno 30 livelli di carico che offrono una capacità di stoccaggio di 15.360 contenitori. In questo magazzino coesistono due tipologie di contenitori: da un lato quelli da 600 x 400 x 420 mm e, dall’altro, da 600 x 400 x 120 mm, con un peso massimo unitario di 50 kg.
In ognuna delle corsie circola un trasloelevatore che consente di gestire automaticamente l’entrata e l’uscita della merce. Nella parte frontale del magazzino, è presente un circuito di rulliere che collega le corsie di stoccaggio con due postazioni di picking e una di riapprovvigionamento.
Sia le rulliere che le postazioni di picking sono state progettate appositamente per operare con entrambi i modelli di contenitori.
I transelevatori forniscono la merce alle postazioni di picking e, subito dopo, gli operatori estraggono gli articoli e li inseriscono nel relativo ordine. I dispositivi put-to-light indicano i contenitori in cui vanno introdotti gli articoli e gli operatori confermano che hanno eseguito l'operazione premendoil pulsante a lato del display. Gli ordini vengono preparati a ondate, vale a dire che vengono preparati vari ordini contemporaneamente.
Easy WMS e Galileo
I cinque magazzini di Porcelanosa Gruppo sono gestiti dal software di gestione dei magazzini (SGM) Easy WMS di Mecalux. Questo coordina e gestisce tutte le fasi operative, dal ricevimento della merce (identificando e convalidando i prodotti provenienti dalla produzione o dall’esterno) e lo stoccaggio in base ai criteri di consumo e rotazione dei prodotti, fino alla preparazione degli ordini e alla spedizione, raggruppando i pallet in base all’ordine o alla destinazione.
Easy WMS di Mecalux è in grado di migliorare la qualità del servizio di Porcelanosa Gruppo e fornire un risparmio in termini di costi, incrementando la redditività del magazzino. Inoltre, è un sistema scalabile, che può ampliare o ridurre le risorse e la potenza in base ai requisiti dell’azienda.
Trattandosi di magazzini completamente automatici, è stato implementato il software di controllo Galileo di Mecalux, che gestisce gli spostamenti eseguiti dai dispositivi di movimentazione per eseguire le operazioni di trasferimento e stoccaggio (trasloelevatori, rulliere, elevatori e navette).
A prova di futuro
Porcelanosa Gruppo, leader mondiale del suo settore, ha introdotto le tecnologie più all'avanguardia in tutti i suoi processi logistici. Mecalux ha contribuito alla sua crescita nel corso gli anni eseguire le operazioni di trasferimento e stoccaggio suoi magazzini.
Questi magazzini soddisfano di gran lunga le esigenze espresse inizialmente da Porcelanosa Gruppo. Offrono una grande capacità di stoccaggio, vantano i mezzi di sollevamento più moderni e i suoi cicli operativi sono molto veloci ed efficienti.
I centri logistici di Vila-real sono predisposti per la crescita futura, con il variare della domanda. E quando arriverà il momento di aumentare la capacità di stoccaggio, ampliare il circuito di rulliere e integrare ulteriori postazioni di picking, sarà possibile procedere senza interrompere il ciclo operativo.
Dal canto suo, il software Easy WMS di Mecalux accompagnerà sempre l'azienda, adeguandosi ai cambiamenti, alle nuove esigenze e all'aumento della produzione di Porcelanosa Gruppo.
Negli ultimi anni, l’azienda ha sperimentato un’espansione senza precedenti e ha rinforzato la sua leadership nel mondo. Con la collaborazione di Mecalux, ha potuto trarre profitto dall'automatizzare dei suoi magazzini e incrementare la produttività al massimo per affrontare questa sfida.
Magazzino di Venis | |
---|---|
Anno di costruzione: | 2011 |
Superficie di stoccaggio: | 8.000 m² |
Capacità di stoccaggio: | 65.000 posti pallet |
Numero di trasloelevatori: | 10 |
Altezza del magazzino: | 31 m |
Galleria
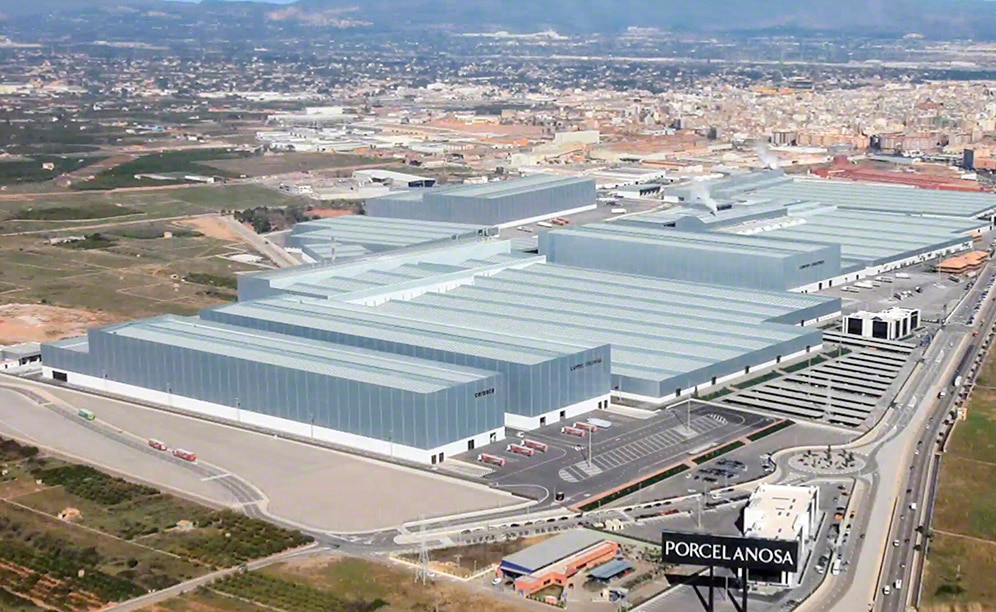
Il complesso logistico di Porcelanosa Gruppo è composto da cinque centri logistici con magazzini automatici di grande capacità
Consultate un esperto