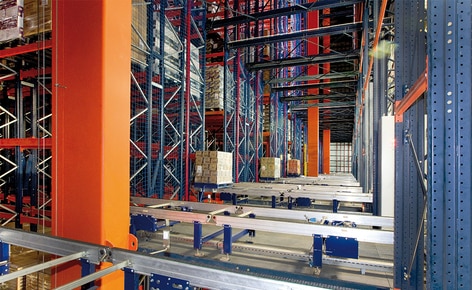
La compagnia alimentare Grupo Siro ha moltiplicato la sua capacità e produttività con un magazzino automatico autoportante alto 35,5 m
Grupo Siro continua a crescere con un gran magazzino automatico autoportante
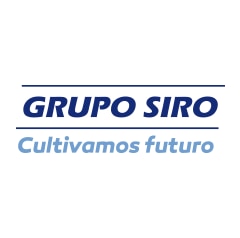
Mecalux ha costruito un magazzino autoportante di grandi dimensioni completamente automatizzato per Grupo Siro, una delle maggiori aziende nel settore alimentare in Spagna. Questo innovativo centro logistico si inquadra nell'ottica del gruppo che punta su soluzioni efficaci per le proprie esigenze, attraverso le nuove tecnologie come fonte di efficienza e crescita sostenibile.
Chi è Grupo Siro
Grupo Siro è uno dei produttori più importanti in Spagna di biscotti, pasta, pane a fette, prodotti da forno e cereali.
Fondato nel 1991, con l'acquisizione di Galletas Siro da Danone, da allora ha sempre scelto l'innovazione e l'uso della tecnologia in tutti i suoi processi operativi, per offrire prodotti della più alta qualità al miglior prezzo.
Attualmente, produce oltre 300 prodotti diversi e vanta 13 centri produttivi, un magazzino logistico, un centro di ricerca, sviluppo e innovazione, un centro di valorizzazione dei sottoprodotti, due centri direzionali e la sede della Fondazione Grupo Siro.
Esigenze del cliente
L'azienda è cresciuta notevolmente negli ultimi anni, soprattutto grazie all'enorme domanda del suo cliente principale: la catena di supermercati Mercadona.
A un certo punto, tale crescita, e il conseguente aumento della produzione, hanno incrementato le esigenze di spazio dei suoi magazzini, ubicati generalmente all'interno delle proprie fabbriche. Per mantenere il ritmo di produzione, la società ha optato in un primo momento per magazzini esterni, ma ciò rendeva difficile la coordinazione della sua catena logistica e incrementava i costi di gestione.
Dopo aver deciso di adottare soluzioni efficienti per le sue esigenze e potenziare la sua crescita, Grupo Siro ha affidato a Mecalux la costruzione di un nuovo centro logistico nella sua sede centrale a Venta de Baños (Palencia) con due premesse molto chiare: migliorare la capacità di stoccaggio delle sue fabbriche e promuovere l'efficienza e la produttività dell'azienda.
La soluzione proposta
L’ufficio tecnico di Mecalux, in collaborazione con il team logistico di Grupo Siro, ha analizzato dettagliatamente esigenze, vincoli e possibilità, per trovare alla fine la soluzione più idonea: la costruzione di un magazzino autoportante alto 36 m, servito da trasloelevatori e rulliere controllati dal software di gestione magazzini Easy WMS di Mecalux.
Il centro logistico è strategicamente ubicato in una circonferenza di 3 km di raggio, nella quale si trovano quattro delle sue principali fabbriche e a meno di 100 km di distanza da altre tre, agevolando e sveltendo il trasporto del carico tra le fabbriche e il centro logistico.
Il flusso di movimentazione è molto intenso e continuo, per questo sono state installate due baie di ricevimento su un lato del magazzino, separate dalle nove baie di spedizione per non creare interferenze tra i due cicli operativi, con un ampio spazio che consente un movimento più dinamico delle manovre di trasporto e di prelievo dai camion.
L'edificio annesso al magazzino è costituito da due piani differenti, per organizzare in modo ottimale i diversi cicli operativi che vi si effettuano:
- Il piano inferiore è destinato soprattutto al ricevimento e alla spedizione della merce, con un'ampia zona di precarico a terra.
- Al piano superiore, i pallet provenienti dalle baie del livello inferiore entrano nel magazzino. Vi è inoltre un'area riservate alle operazioni di picking.
Il magazzino
Il magazzino possiede dimensioni considerevoli: 102 m di lunghezza, 57 m di larghezza e 35,5 m di altezza, il massimo consentito dalle normative locali. È distribuito su otto corsie con scaffalature a doppia profondità su entrambi i lati, ciascuna con 14 livelli di carico di diverse altezza adattate ai formati di pallet del Grupo Siro: cinque livelli per europallet da 1.400 mm di altezza, otto da 2.000 mm e uno da 2.500 mm. Le unità di carico hanno un peso medio di 800 kg e uno massimo di 1.000 kg.
Ciascuna corsia è dotata di un trasloelevatore bicolonna con forche telescopiche e una cabina di manutenzione a bordo della culla. Questa macchina si occupa di stoccare ogni pallet nella sua relativa ubicazione, in funzione delle sue dimensioni e della sua rotazione.
L'automazione del magazzino si completa con due circuiti di rulliere: uno al piano terra, dove si depositano i pallet destinati alle spedizioni, e un altro al piano superiore, a 6,7 m di altezza, che collega tutte le entrate e tutte le uscite alla zona di picking.
Nella parte superiore del magazzino sono stati sfruttati gli spazi liberi tra le tralicciature, per posizionare le condutture dell'aria condizionata che regolano la temperatura di tutto l'impianto e distribuiscono correttamente l'aria.
All'esterno dell'edificio, nella parte posteriore, sono stati adibiti quattro dispositivi di pompaggio del sistema antincendio e un serbatoio di acqua con capacità sufficiente per le dimensioni del magazzino. All'interno si trovano gli sprinkler e i sensori che evitano eventuali principi di incendio.
Il pianoterra
Distribuzione del pianoterra:
- Baia di scarico automatica
- Baia di scarico convenzionale
- Baie di carico (9 in totale)
- Zona di controllo dell'entrata pallet ed elevatore
- Uscite dei pallet dal magazzino
- Zone di precarico a terra
- Circuito virtuale di carrelli LGV
- Accumulo di pallet vuoti
- Ricevimento e ricondizionamento dei pallet in entrata
Entrata della merce
L'entrata della merce proveniente dai centri di produzione più vicini avviene dalle due baie di ricevimento, una di esse con scarico automatico dei camion e l'altra manuale, con carrelli o transpallet.
L'area di scarico ha una capacità di accumulo di due camion completi, ossia un totale di 66 pallet che vengono inviati alla zona di controllo dove si convalida il loro stato.
Tutti i pallet passano obbligatoriamente per l'area di controllo, dove si verifica che siano in buono stato e il loro peso e le loro misure corrispondano ai requisiti di qualità del magazzino.
Se il pallet va bene, il sistema di controllo trasmette il comando per far proseguire il tragitto fino all'elevatore, che lo trasporterà al piano superiore, e quindi entrerà nel magazzino automatico.
Quando il pallet non supera il controllo, può essere inviato a tre zone differenti, secondo l'anomalia rilevata:
- La zona di ricondizionamento.
- L'area di accumulo, dove si correggono i debordi che superano i limiti previsti.
- Rimontaggio pallet: quando le unità di carico dispongono di una base inadeguata, si posizionano su un'altra in buono stato mediante dei sollevatori. Questi pallet tornano all'area di controllo e sono verificati di nuovo, prima di accedere al piano superiore.
Il pallet difettoso che non può essere corretto verrà trasportato alla zona di uscita ed espulso dal circuito.
I pallet che sono stati ricondizionati attraversano nuovamente la postazione di controllo per verificare di nuovo che osservino i requisiti del magazzino.
Si deve garantire che la merce introdotta nel magazzino automatico sia adeguata e si deve verificare che il carico non debordi più del previsto.
Uscite dal magazzino / Spedizioni
I carrelli elevatori a guida automatica (LGV) movimentano i pallet che escono dal magazzino, raccogliendoli nei punti di uscita di ciascuna corsia di stoccaggio e trasportandoli alla zona di prelievo assegnata in una delle nove baie di carico, seguendo un circuito virtuale precedentemente programmato.
Il carrello definisce la sua traiettoria emettendo un segnale laser che rimbalza su deflettori posizionati in punti vicini al percorso. Il sistema di gestione può conoscere con esattezza la sua posizione e trasmette l’ordine di dirigersi alle stazioni di ricarica quando il livello delle batterie giunge a un limite stabilito. Essendo un collegamento completamente automatico, in questo processo non è necessario l'intervento umano.
Solo il caricamento dei camion è eseguito dagli operatori, che aiutati da transpallet introducono la merce nel camion assegnato dal software di gestione magazzini, in base al numero di ordine, il percorso da effettuare, il cliente ecc.
Il personale conferma ogni operazione ed esecuzione degli ordini mediante un terminale a radiofrequenza.
Il piano superiore
Entrata magazzino
La merce proveniente dalle baie di ricevimento, una volta superata l'area di controllo, accede al primo piano attraverso l'elevatore.
Quindi una rulliera principale distribuisce le referenze attraverso rulliere di entrata alle diverse corsie di stoccaggio.
È un circuito a una sola direzione, per il quale si muovono anche i pallet che escono dalle corsie e si dirigono alle zone di picking.
Organizzazione del piano superiore:
- Elevatore
- Circuito interno del magazzino
- Rulliere di entrata o uscita di ogni corsia
- Navetta della zona di picking
- Postazioni di picking
- Zona di imballaggio e ricondizionamento
- Rulliera principale di entrata al magazzino
Zona di picking
Sono inoltre state installate due postazioni di picking unite, nelle quali ogni operatore può preparare due ordini contemporaneamente. La zona è preparata per essere ampliata in futuro se le esigenze di Grupo Siro lo richiedono.
Le postazioni di picking sono posizionate su rulliere. Su entrambi i lati dell'operatore si trovano piattaforme elevatrici idrauliche che si regolano su una posizione ergonomica per movimentare la merce. In questo modo, la preparazione degli ordini è molto più agile.
Ogni postazione di picking dispone di un circuito ad accumulo. Sono anche stati adibiti sollevatori e dispenser di pallet che riforniscono l'area, oltre a stazioni di prelievo di pallet che sono usciti dal magazzino e non hanno un vano libero nel circuito della postazione assegnata.
Una volta terminato l'ordine, il pallet si inserisce nel circuito di rulliere che, dopo averlo fatto passare per la fasciatrice, lo trasporterà di nuovo al magazzino, fino a quando il sistema di gestione ne ordinerà la spedizione.
Il software
Il magazzino è gestito mediante il software Easy WMS di Mecalux e comunica costantemente con il sistema di pianificazione di risorse di Grupo Siro, per controllare, coordinare e informare di tutti i processi logistici e i cicli operativi che avvengono all'interno del magazzino.
Il software è concepito per avere un carattere pratico e operativo, oltre a compiere le seguenti funzioni:
- Controllo assoluto sulla gestione del magazzino.
- Gestione dell'entrata e dell'uscita della merce dalle baie di carico e scarico.
- Sistemazione strategica delle unità di carico nel magazzino, seguendo un controllo delle corsie e delle loro ubicazioni.
- Registrazione e regolazione dello stock in tempo reale.
- Progettazione dell'ordine di uscita della merce e suo successivo carico nel camion mediante un terminale a radiofrequenza.
- Ottimizzazione delle operazioni in conformità con il percorso di picking.
- Comunicazione diretta con il fornitore logistico di Grupo Siro.
- Coordinazione di tutti i dati anagrafici (articoli, proprietari, fornitori, clienti ecc.).
Vantaggi per Grupo Siro
- Risparmio sui costi di gestione: l'eliminazione dei magazzini esterni e la centralizzazione delle operazioni nello stesso centro logistico consente un aumento della produttività e un veloce ritorno sull'investimento.
- Massima capacità: la grande altezza del magazzino e l'uso di trasloelevatori ha permesso di moltiplicare la capacità di stoccaggio di Grupo Siro, adattandosi alla crescita della sua produzione.
- Gestione completamente automatizzata: Grupo Siro ha integrato e coordinato i suoi cicli operativi di ricevimento, stoccaggio, picking e spedizione di merci in un solo spazio, con la gestione e il controllo di Easy WMS, ottimizzando il rendimento di tutta la sua catena logistica.
- Incremento della sicurezza: i magazzini automatici offrono la massima protezione per gli operatori e la merce, contribuendo in questo modo all'obiettivo dell'azienda di promuovere processi efficienti che garantiscano sempre la sicurezza delle persone.
Centro logistico automatico di Grupo Siro, Spagna | |
---|---|
Capacità totale: | 40.320 posti pallet |
Dimensioni del pallet: | 800 x 1.200 x 1.400 / 2.000 / 2.500 mm |
Peso massimo del pallet: | 1.000 kg |
N. di scaffalature: | 16 a doppia profondità |
N. di corsie: | 8 |
Numero di trasloelevatori: | 8 |
N. di livelli di carico: | 14 |
Lunghezza del magazzino: | 101 m |
Larghezza del magazzino: | 57 m |
Altezza del magazzino: | 33,5 m |
Galleria
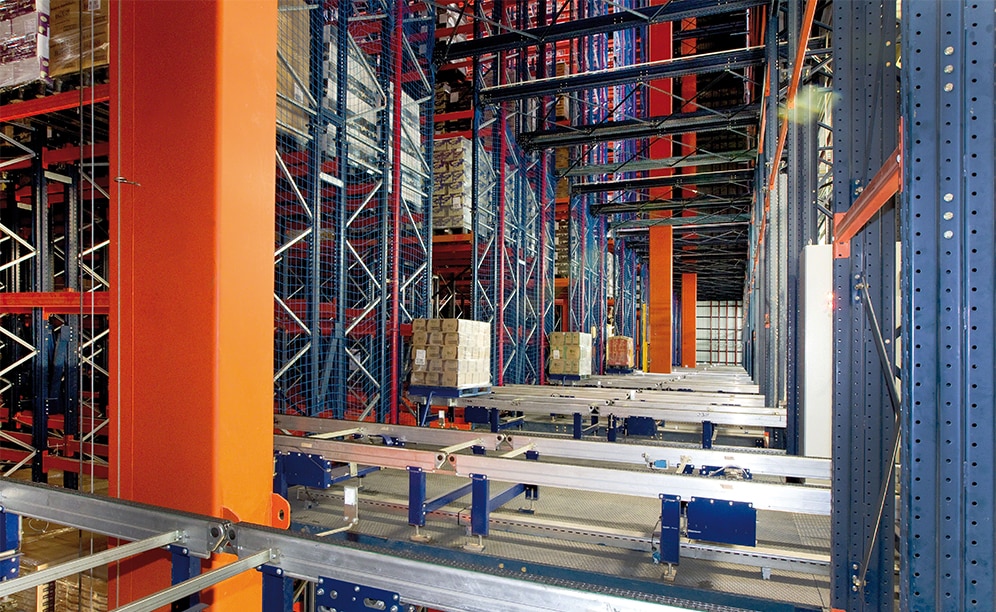
Mecalux has built a fully automated, super-sized clad-rack warehouse for Grupo Siro
Consultate un esperto