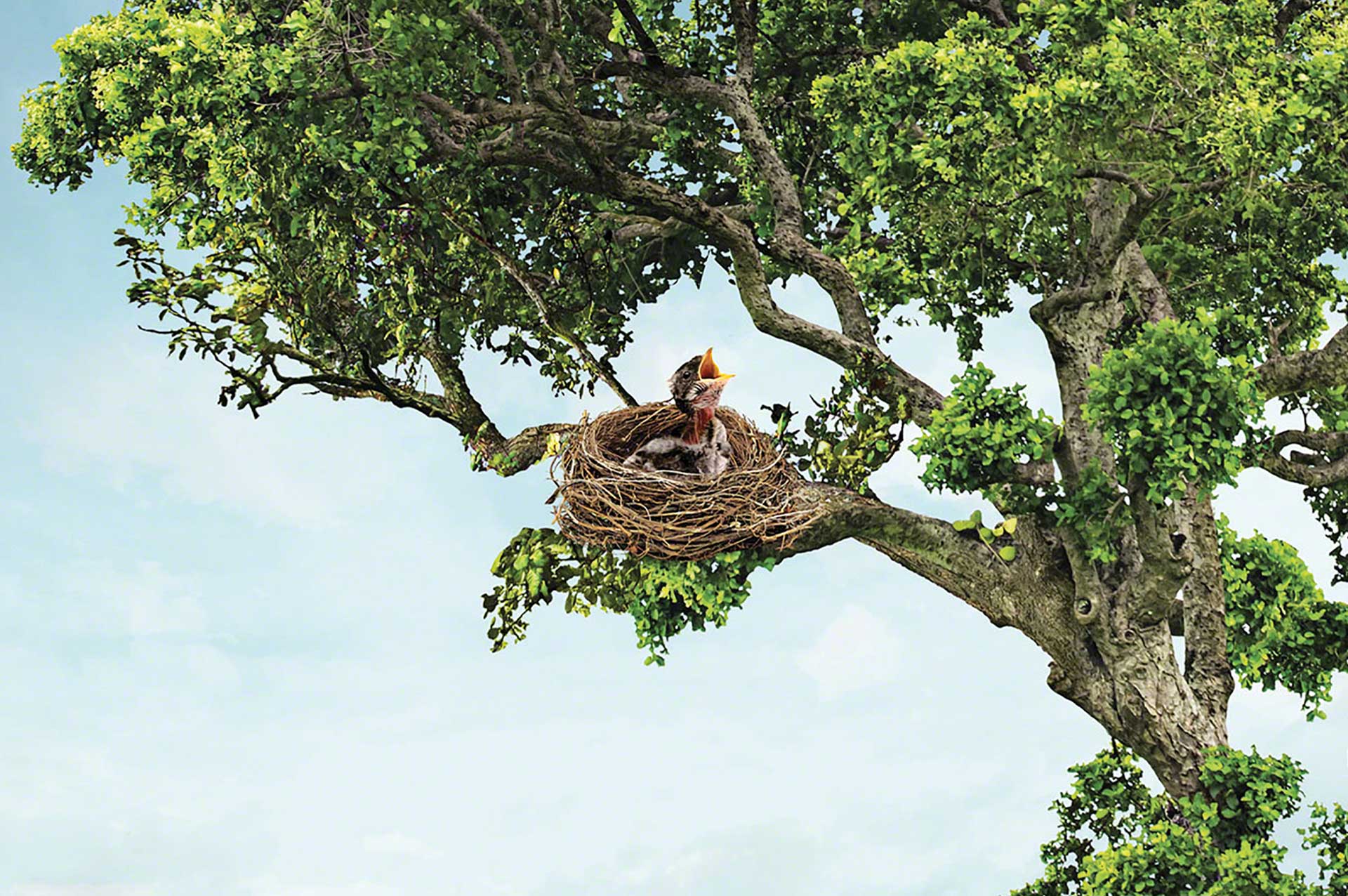
Konya Şeker installa un magazzino automatico in una zona sismica
Konya Şeker, il principale produttore di zucchero della Turchia, connette il suo stabilimento di produzione con un magazzino automatico antisisimico da 38 m.
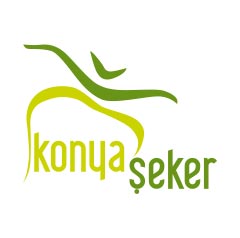
Konya Şeker, il principale produttre di zucchero della Turchia, ha modernizzato la logistica del suo centro a Çumra con un magazzino automatico antisismico da 38 m. Connesso con le linee di produzione, il magazzino robotizzata velocizza la distribuzione giornaliera di 2.000 pallet di cioccolato e biscotti.
Konya Şeker: il più grande produttore di zucchero della Turchia
Konya Şeker è un'azienda turca che produce e commercializza zucchero e altri derivati. La società produce anche un'ampia varietà di dolci a base di zucchero, tra cui cioccolatini, biscotti e halvas (dolci orientali con pasta di sesamo). Dal 2008, Konya Şeker fa parte del gruppo Anadolu Birlik Holding (ABH), che riunisce industrie di diversi settori come quello alimentare, agricolo, energetico e chimico. Fondata nel 1954, Konya Şeker può contare su 45 installazioni, 900.000 agricoltori e un team professionale di oltre 10.000 persone.
SFIDE
|
SOLUZIONI
|
VANTAGGI
|
---|
Negli ultimi decenni, Konya Şeker ha completamente rinnovato le sue operazioni logistiche e produttive con le più recenti tecnologie del mercato e un deciso impegno nell'automazione dei processi robotizzati. Questa modernizzazione della supply chain ha permesso all'azienda di aumentare la produzione fino a diventare il più grande produttore di zucchero in Turchia e di far fronte a un ambizioso processo di espansione. Oggi l'impresa dispone di 45 siti produttivi in cui produce circa il 22% dello zucchero consumato in Turchia. Konya Şeker è anche leader nel mercato delle patate surgelate.
Nella piccola città di Çumra, appena fuori dalla città di Konya, l'azienda ha il più grande zuccherificio della Turchia: si estende su 260 ettari e ha 27 linee di produzione. "Negli ultimi anni abbiamo raddoppiato la nostra produzione annuale di zucchero, portandola a 435.500 tonnellate. Tutti i macchinari e le attrezzature sono stati forniti dai migliori fornitori di tecnologia all'avanguardia in Europa. Inoltre, questo è l'unico zuccherificio al mondo che può rifornirsi di materie prime nel raggio di 20 km", afferma Kerim Başaran, Responsabile del magazzino automatico di Konya Şeker.
Lo stabilimento di Çumra ospita il centro di produzione del suo marchio di cioccolatini e biscotti. "I nostri impianti di produzione del cioccolato Torku, dotati delle più moderne tecnologie, riforniscono il mercato locale e ci permettono di esportare i nostri prodotti in 74 Paesi, tra cui la Svizzera, punto di riferimento mondiale per il cioccolato", spiega Başaran.
Qualche anno fa, Konya Şeker ha ampliato e diversificato il portafoglio prodotti di Torku con cioccolatini, latticini, carne, dolci, olio e aceto, tra gli altri. Di conseguenza, la società ha dovuto dare priorità alla logistica per far fronte all'incremento della produzione. Inizialmente, ha gestito sia le materie prime che i prodotti finiti in un magazzino tradizionale. Tuttavia, la necessità di ridurre i tempi di entrata e uscita delle merci ha portato l'azienda a investire nella tecnologia intralogistica.
Seguendo la strategia di ammodernamento delle proprie strutture, Konya Şeker ha costruito un magazzino automatico autoportante gestito dal software Easy WMS di Mecalux, con il quale distribuisce 2.000 pallet al giorno. In grado di ospitare 48.000 pallet di biscotti e cioccolatini, il magazzino è integrato con il centro di produzione, facilitando lo scambio autonomo di materie prime e prodotti finiti pronti per la distribuzione.
Oltre ad aumentare il rendimento, la tecnologia ha contribuito a massimizzare la qualità dei prodotti dolciari, garantendo il rispetto di rigorosi protocolli di sicurezza e igiene. "Le nostre priorità sono produrre cioccolato naturale e privo di additivi, preservandone le proprietà. Per raggiungere questo obiettivo, è essenziale garantire la conformità alla legislazione pertinente", manifesta Başaran.
Un magazzino automatico in una zona sismica
La maggior parte della Turchia si trova sulla placca tettonica anatolica che si trova tra le placche eurasiatica, araba e africana. L'attrito tra queste placche rende la Turchia una delle regioni più sismicamente attive del pianeta.
Il magazzino di Konya Şeker ha una struttura autoportante, vale a dire che le scaffalature stesse sostengono il proprio peso, quello delle coperture verticali e del tetto, oltre a quello delle merci. La sua progettazione ha tenuto conto di alcuni fattori che interagiscono con la sua struttura, come la forza del vento e, in questo caso specifico, il grado sismico corrispondente alla zona di installazione e alle normative locali in vigore.
La costruzione di un magazzino alto 38 metri in una località ad alto grado sismico come Konya ha rappresentato una sfida per il dipartimento di ingegneria strutturale di Mecalux e ha richiesto un'enorme precisione nell'assemblaggio. Le scaffalature sono state rinforzate e sono stati utilizzate spalle centrali più robuste per assorbire le forze dinamiche causate da eventuali movimenti sismici.
Massimo rendimento nel magazzino di Konya Şeker
"Grazie all'automazione abbiamo ridotto i tempi di stoccaggio e recupero delle nostre merci", sostiene Başaran. Il magazzino automatico di Konya Şeker è composto da sette corridoi lunghi 138 m con scaffalature a doppia profondità. Per stoccare ed estrarre i pallet, i trasloelevatori di Mecalux installati in ogni corsia sono dotati di forche telescopiche in grado di accedere alla seconda posizione di tutti i livelli. Queste macchine, che seguono gli ordini di Easy WMS, lavorano a una velocità di traslazione di 220 m/min e di 64 m/min in sollevamento.
Due dei corridoi del magazzino di Konya Şeker sono destinati alle materie prime e ai prodotti di imballaggio, mentre gli altri cinque corridoi ospitano i prodotti finiti. Tre di essi operano a una temperatura controllata di 15 °C per mantenere la consistenza, il gusto e il profumo dei cioccolatini, mentre altri due corridoi operano a temperatura ambiente.
Le referenze vengono collocate nelle ubicazioni in base alle loro dimensioni e ai criteri di rotazione A, B e C gestiti da Easy WMS. I prodotti a più alta rotazione sono collocati a un'estremità del magazzino, più vicini ai trasportatori in entrata e in uscita. Quelli a più bassa rotazione, invece, sono collocati più lontano, all'estremità opposta dei corridoi. In questo modo si ottimizzano i movimenti dei trasloelevatori.
Collegamento automatico con la produzione
Uno dei principali vantaggi dell'automazione del magazzino di Konya Şeker è l'integrazione con il centro di produzione, a sua volta composto da due aree distinte: una riservata ai cioccolatini e l'altra ai biscotti.
Per garantire un flusso ininterrotto di movimenti, un tunnel sopraelevato (a un'altezza di 6 m) collega le uscite della produzione di cioccolato e biscotti con il magazzino. All'interno, un circuito di trasportatori automatici corre lungo il lato dell'installazione logistica fino a raggiungere la parte anteriore. Grazie alla loro capacità di accumulo, i pallet possono rimanere temporaneamente sui trasportatori, in attesa di entrare nel magazzino, in modo ordinato e senza doverli appoggiare sul pavimento. Successivamente, gli elevatori situati all'inizio e alla fine del tunnel trasferiscono la merce tra i diversi livelli.
L'impianto di picking automatizzato di Konya Şeker
Konya Şeker è responsabile del rifornimento quotidiano di supermercati e negozi in Turchia. A questo scopo, un edificio a due piani si trova a un'estremità del magazzino. Il piano superiore è utilizzato per la preparazione degli ordini e il piano inferiore per la spedizione.
Il piano di picking dispone di quattro blocchi di canali a gravità per i prodotti più richiesti. Una navetta automatica alimenta ogni canale, che può contenere fino a un massimo di tre pallet della stessa referenza, il che significa che c'è sempre merce di riserva. Nella parte più bassa dei canali, gli operatori accedono direttamente ai pallet e prelevano le scatole che compongono ogni ordine. Si muovono lungo i corridoi assistiti da commissionatori e individuano le referenze indicate dal software di gestione del magazzino di Mecalux tramite un terminale a radiofrequenza.
Davanti ai corridoi di stoccaggio, i nastri trasportatori spostano le SKU richieste verso tre stazioni di picking per gli articoli a bassa richiesta. Gli operatori possono prelevare fino a dodici ordini contemporaneamente.
Una volta chiusi gli ordini, i pallet passano alla fasciatrice, vengono poi stoccati in attesa che Easy WMS assegni loro un percorso e ne ordini l'invio all'area di spedizione.
Il piano inferiore dell'edificio annesso al magazzino è dedicato alle merci in uscita. Una navetta le classifica e le mette in sequenza in 26 canali a gravità di precarico. I pallet vengono raggruppati in ogni canale, tenendo conto se fanno parte dello stesso ordine o dello stesso percorso, e vengono preparati fino al caricamento sui camion.
Il software di gestione magazzino di Mecalux svolge un ruolo chiave nell'intero processo logistico di Konya Şeker: "Con Easy WMS abbiamo un controllo più rigoroso dei 48.000 pallet che abbiamo nel magazzino automatico e ci aiuta ad eseguire tutte le operazioni rapidamente e senza errori", dice Başaran.
Per migliorare la gestione delle merci, il software comunica con l'ERP di Konya Şeker. L'ERP notifica in anticipo a Easy WMS gli articoli che arrivano dalla produzione al magazzino automatico, in modo da poter assegnare le ubicazioni più rapidamente.
Konya Şeker porta la sua logistica al livello di un'azienda leader
"Torku si è guadagnata il riconoscimento dei consumatori con i suoi prodotti 100% naturali, sicuri e di alta qualità. Li produciamo controllando l'intero processo dal seme alla tavola, garantendo la loro purezza e il lavoro degli agricoltori dell’Anatolia", manifesta Başaran.
Il magazzino automatico, alto 38 metri, ha rappresentato un punto di svolta nella supply chain di Konya Şeker e, in particolare, dei cioccolatini e biscotti Torku. L'automazione e la digitalizzazione logistica sono strumenti fondamentali per l'impresa per raggiungere i propri obiettivi. Grazie a queste tecnologie, l'azienda mantiene una tracciabilità completa dei suoi prodotti e ha migliorato l'efficienza dei suoi processi operativi con un obiettivo chiaro: garantire la distribuzione di 2.000 pallet al giorno in 74 Paesi.
Con Easy WMS abbiamo un controllo più rigoroso dei 48.000 pallet che abbiamo nel magazzino automatizzato e ci aiuta a eseguire tutte le operazioni rapidamente e senza errori.
Galleria
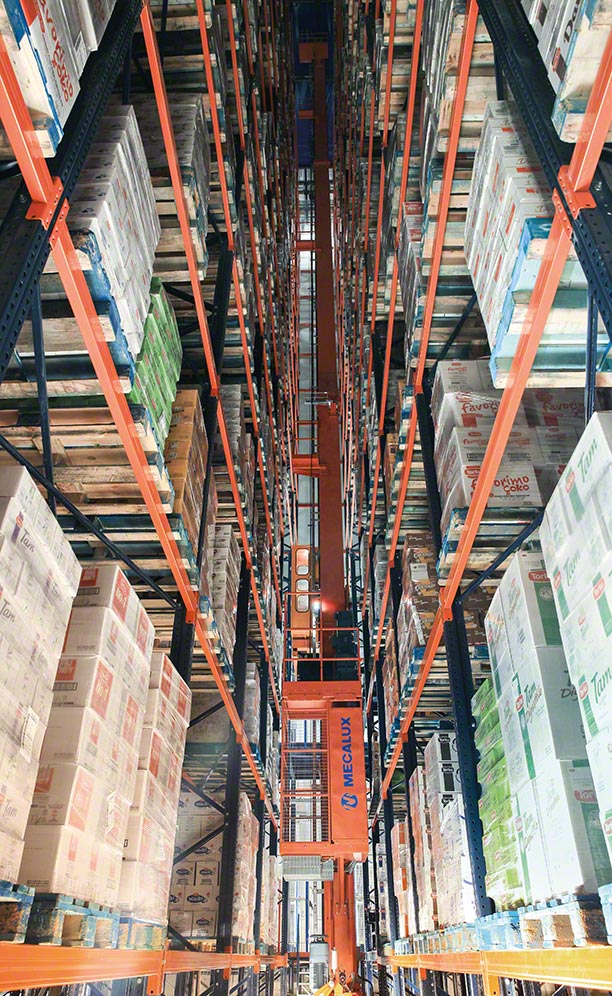
Il trasloelevatore muove i pallet all'interno delle corsie di stoccaggio di Konya Şeker
Consultate un esperto