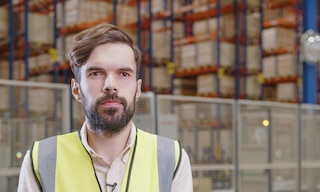
Intervista a Pavol Masarovič, Direttore opertivo di IKEA Components Slovacchia
“L'automazione del magazzino è stata completata senza doverne arrestare il funzionamento”
Riguardo IKEA Components
IKEA Components, filiale della multinazionale svedese IKEA responsabile dell'imballaggio e della consegna di accessori e componenti per mobili, ha automatizzato il suo magazzino di Malacky (Slovacchia) con trasloelevatori trilaterali senza interrompere l'attività in alcun momento. Inoltre, ha implementato il software di gestione magazzini Easy WMS per aumentare l'efficienza.
Mecalux intervista a Pavol Masarovič, Direttore operativo di IKEA Components Slovacchia. La filiale ha automatizzato il suo magazzino di Malacky (Slovacchia) senza interrompere l'attività in alcun momento. Inoltre ha incrementato la sua capacità di completare gli ordini.
-
IKEA è presente in 62 mercati e ha più di 450 negozi. Com'era la logistica di IKEA Components prima dell'automazione?
Fino ad allora, tutta la nostra area di spedizione operava in modo completamente tradizionale. Cioè, tutti i movimenti e i trasferimenti di pallet avvenivano con carrelli elevatori o in scaffalature a corsie strette. Portavamo i pallet dall'area di produzione e li stoccavamo in magazzino. Questo sistema richiedeva più tempo, più attrezzature per la movimentazione dei materiali e più colleghi che svolgevano gli stessi compiti, quindi abbiamo deciso di automatizzare alcuni aspetti.
-
Mecalux ha automatizzato il magazzino di IKEA Components a Malacky senza interrompere le operazioni. Come è stato sviluppato questo progetto?
Il requisito principale che abbiamo posto a Mecalux è stato quello di preparare e progettare l'intero processo in modo tale da non alterare il funzionamento del magazzino durante la sua installazione. È una richiesta che abbiamo fatto ancora prima di iniziare. Non c'era la possibilità di chiudere completamente l’impianto.
Il progetto è stato suddiviso in quattro fasi. In ogni fase sono stati installati tre trasloelevatori trilaterali ed è stato ampliato il circuito di trasportatori. Suddividendo l'intervento in diverse fasi, siamo stati in grado di completare l'intervento intaccando solo il 25% della capacità totale durante ogni fase. Pertanto, l'impatto di questi lavori è stato minimo e non ha influito sulla nostra attività quotidiana.
Ora ci concentriamo sul mantenimento delle scorte mentre l'automazione si occupa della movimentazione dei pallet
-
Quali vantaggi ha portato il magazzino automatico a IKEA Components?
Ci offre maggiore flessibilità ed efficienza, a partire dalla movimentazione dei pallet. Prima dovevamo fare tutto manualmente, ma oggi non dobbiamo preoccuparci di spostare le merci perché l'automazione lo fa per noi. Così possiamo concentrarci sul mantenimento delle scorte. Avere i prodotti in un magazzino automatizzato ci dà una migliore visibilità dell'inventario ed è anche più difficile commettere errori rispetto alla gestione tradizionale.
Il sistema è facile da controllare perché è gestito con il software di gestione magazzino Easy WMS. Il software controlla tutti i processi e, quando dobbiamo consegnare i pallet ai nostri clienti, invia le istruzioni. Successivamente, i pallet lasciano il magazzino in modo autonomo.
Abbiamo visto i vantaggi dei sistemi di magazzino automatizzati, soprattutto durante il periodo della pandemia. Abbiamo avuto alcuni colleghi in malattia ma, avendo un magazzino che non dipendeva così tanto dagli operatori, siamo stati in grado di continuare a soddisfare le richieste dei nostri clienti e di inviare tutti i pallet che richiedevano.
-
Che percorso fa un pallet dal momento in cui arriva fino a quando lascia la struttura?
Abbiamo completato l'installazione intaccando solo il 25% della capacità totale in quattro fasi Tutti i pallet che arrivano al magazzino di distribuzione provengono dalla nostra area di produzione. I veicoli a guida automatica sono responsabili di prelevarli dalla nostra linea di chiusura dei pallet. Poi, proseguono il loro viaggio lungo il nastro trasportatore ed entrano nella postazione di controllo in entrata (PIE) installata da Mecalux. Lì, Easy WMS sceglie l’ubicazione della merce e ordina di spostare automaticamente il pallet in una delle dodici corsie di stoccaggio. In seguito, quando il pallet viene richiesto e dobbiamo inviarlo a un cliente, l'intero processo si avvia roboticamente non appena un operatore dà l'ordine. Infine, i pallet partono da uno o dall'altro nastro trasportatore, a seconda della loro destinazione finale, e raggiungono le diverse aree di carico seguendo il percorso più breve possibile.
-
Qual è la sua valutazione di questa trasformazione intralogistica?
Il progetto Malacky è durato quasi tre anni e ci ha posto di fronte a diverse sfide, ma siamo riusciti a risolverle tutte in modo molto professionale e senza allontanarci dall'obiettivo di migliorare la nostra efficienza. La collaborazione con Mecalux è stata molto professionale, il rapporto molto cordiale e alla fine abbiamo portato a termine il compito con successo. Sono state coinvolte molte persone, sia da parte loro che da parte nostra. Nel complesso, è stato un grande progetto per tutti noi, in cui abbiamo imparato qualcosa di nuovo e acquisito competenze ed esperienze che potremo applicare in futuro.