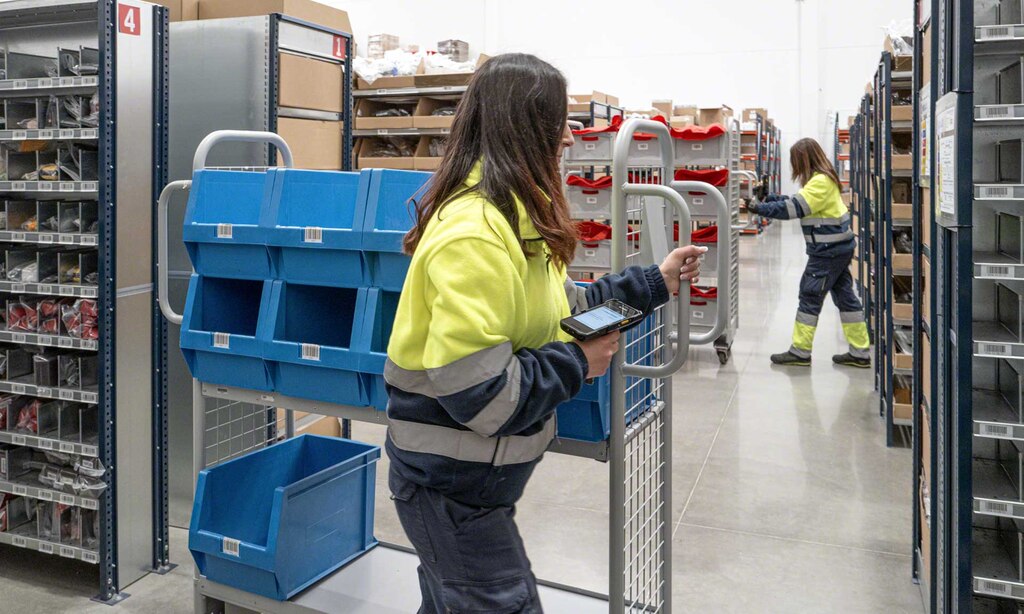
RICERCA LOGISTICA
Di Shuya Zhong, Vaggelis Giannikas, Jorge Merino, Duncan McFarlane, Cheng Jun e Shao Wei
Il picking e il packing sono due processi chiave nel completamento degli ordini. Il picking prevede la raccolta di vari articoli da diverse ubicazione del magazzino e il loro confezionamento in imballaggi come scatole, sacchi o colli. Entrambe le operazioni sono cruciali nel determinare il tempo che un ordine trascorrerà nello stabilimento dal momento in cui il cliente acquista una serie di prodotti fino a quando la spedizione è pronta.
In questo studio analizziamo i risultati della pianificazione del picking e del packing nei magazzini di e-commerce. Per stabilirne l'utilità bisogna prendere in considerazione entrambe le attività: il miglioramento di una sola di esse non ha un impatto rilevante, poiché sono intrinsecamente collegate.
Tuttavia, sebbene queste due operazioni siano strettamente collegate tra loro, il prelievo e l'imballaggio sono spesso processi collegati ma indipendenti, svolti da due team di operatori distinti. Analizziamo la gestione congiunta di picking e packing per incrementare le prestazioni dei magazzini rispetto all'organizzazione separata delle due operazioni.
Tre domande chiave
L'obiettivo non è solo quello di migliorare il prelievo e l'imballaggio, ma anche di ridurre i tempi di attesa tra i due processi. Per raggiungere questo obiettivo sono state utilizzate due metriche principali: il tempo di elaborazione dell'ordine (il tempo necessario affinché un singolo ordine sia pronto per la spedizione) e il tempo di ciclo di lavorazione (il tempo necessario al magazzino per elaborare un determinato numero di ordini fino a quando sono pronti per la spedizione).
In un magazzino e-commerce, un ordine viene generalmente classificato in una delle quattro categorie in base al numero di SKU e alla quantità ordinata di ciascuno di essi: 1 referenza-1-articolo, 1 referenza-molteplici-articoli, molteplici-referenze-1-articolo e molteplici-referenze-molteplici-articoli. Questa classificazione influisce sulle ubicazioni a cui recarsi e sui tempi di preparazione e imballaggio.
La ricerca tiene conto anche i diversi livelli di personale assegnato al picking e all'imballaggio. Per valutare i potenziali vantaggi di operare in modo integrato, abbiamo progettato uno studio sperimentale su un'azienda di stoccaggio basato su dati empirici e abbiamo confrontato la pianificazione congiunta di prelievo e imballaggio con la pianificazione individuale attraverso un modello matematico.
Gestire i processi di picking e packing in maniera integrata migliora il rendimento del magazzino
Il modello matematico ha cercato di rispondere a tre domande: Come devono essere raggruppati gli ordini per formare una picking list? Come devono essere organizzati i picker? Come e in che ordine devono essere assegnate le picking list agli incaricati al packing dopo aver completato il picking?
A tal fine, sulla base di studi condotti sull'argomento e sull'attività di una società specifica, abbiamo definito le seguenti caratteristiche di un magazzino. Queste strutture operano con un sistema di preparazione degli ordini a basso livello, in cui i prodotti vengono classificati man mano che vengono prelevati. L'area di picking comprende più corridoi ampi e un magazzino in cui ogni SKU è stoccata in un'unica ubicazione. Gli addetti al picking utilizzano un carrello, che è sempre disponibile, e completano percorsi a S, mentre gli addetti al packing rimangono alla loro postazione di lavoro.
Quattro scenari diversi
Il magazzino manuale studiato è una piattaforma logistica che opera per un'azienda di vendita al dettaglio online. Sono stati analizzati diversi scenari con diversi volumi di ordini. Ognuno di essi richiedeva quantità e referenze diverse ed era inoltre suddiviso tra un numero variabile di picking list.
Tempi di attesa e di esecuzione di metodi con integrazione e senza integrazione con differenti assegnazioni di manodopera
Se si hanno più packer che picker, il risparmio di tempo si ottiene prima di iniziare il prelievo
- Con 300 ordini e un massimo di 24 picking list, il coordinamento di prelievo e imballaggio ha ridotto i tempi di lavorazione e il tempo del ciclo di produzione. Per ottenere questo risultato, il metodo integrato "sacrifica" una parte dell'efficienza del picking per ottenere un significativo risparmio di tempo nella fase di imballaggio.
- Negli scenari relativi a 100-600 ordini distribuiti tra 8 e 48 liste di prelievo, è stato dimostrato che all'aumentare del numero di ordini, i benefici della gestione congiunta di picking e packing tendono a diminuire.
- Studiando 300 ordini con composizioni diverse, in cui varia il rapporto tra 1-referenza-1-articolo, 1 referenza-molteplici-articoli, molteplici-referenze-1-articolo e molteplici-referenze-molteplici-articoli, si osserva che il metodo integrato accresce le prestazioni. Il vantaggio è più significativo quando la complessità delle spedizioni da preparare è moderata.
- Dodici lavoratori sono distribuiti in vari modi per variare il numero di picker e packer nella gestione di 300 ordini con 24 picking list. Quando ci sono più picker che packer, il maggior vantaggio dell'integrazione consiste nella riduzione dei tempi prima di arrivare alla fase di imballaggio. Se gli addetti all’imballaggio sono più di quelli addetti al picking, il risparmio di tempo si verifica prima dell’inizio del picking. Ciò significa che, in alcuni scenari in cui non è possibile accelerare l'imballaggio, organizzare il picking e l'imballaggio insieme non è vantaggioso.
Risultati: wave picking più piccole
I nostri risultati indicano che la pianificazione congiunta di prelievo e imballaggio può ottimizzare le prestazioni in varie condizioni. È stato dimostrato che concentrarsi solo sulle modifiche al picking non garantisce miglioramenti a livello di sistema quando l'imballaggio continua ad agire come collo di bottiglia. Inoltre, piccoli compromessi nella gestione del picking possono generare grandi risparmi di tempo nella fase di imballaggio e aumentare l'efficienza complessiva.
Allo stesso modo, il numero di ordini considerato per la distribuzione del lavoro e i benefici che la pianificazione congiunta può apportare sono inversamente proporzionali. Ciò evidenzia l'importanza di stabilire il numero di ordini da raggruppare prima di avviare qualsiasi processo, come ad esempio un processo di wave picking. Nella pratica, quindi, può essere preferibile optare per più onde di dimensioni ridotte per ottenere i maggiori benefici dalla pianificazione congiunta.
AUTORI DELLA RICERCA:
- SHUYA ZHONG. Professore associato di Logistica e Supply Chain presso l'Università di Bath (Regno Unito).
- VAGGELIS GIANNIKAS. Professore di tecnologia e gestione delle operazioni e direttore del Centre for Smart Warehousing and Logistics Systems dell'Università di Bath (Regno Unito).
- JORGE MERINO. Ricercatore associato presso l'Institute of Manufacturing dell'Università di Cambridge (Regno Unito).
- DUNCAN McFARLANE. Professore di Ingegneria dell'Informazione Industriale presso il Dipartimento di Ingegneria dell'Università di Cambridge e Direttore del Laboratorio di Informazione Distribuita e Automazione dell'Institute of Manufacturing (Regno Unito).
- JUN CHENG. Shenzhen YH Global Supply Chain Co., Ltd (Cina).
- WEI SHAO. Shenzhen YH Global Supply Chain Co., Ltd (Cina).
Pubblicazione originale:
Zhong, Shuya, Giannikas, Vaggelis, Merino, Jorge, McFarlane, Duncan, Cheng Jun, Shao Wei. 2022 "Evaluating the benefits of picking and packing planning integration in e-commerce warehouses". European Journal of Operational Research, 301 (Elsevier).
Versione gratuita disponibile a questo indirizzo.