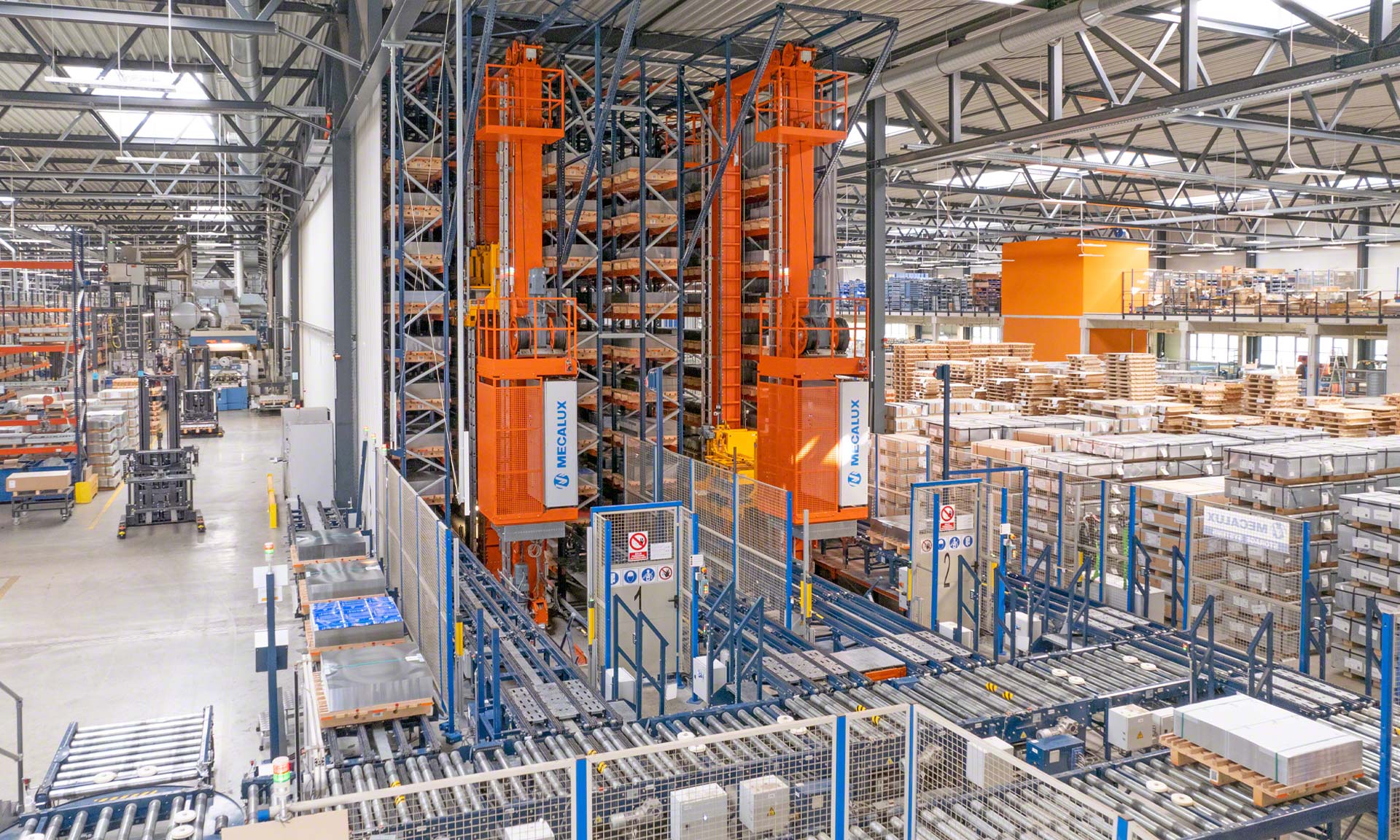
Blechwarenfabrik: la fabbrica di contenitori metallici più moderna d'Europa
Blechwarenfabrik, produttore di lattine in alluminio a Limburgo (Germania), integra i processi produttivi e logistici in un nuovo centro di 63.000 m² completamente automatizzato e digitalizzato.
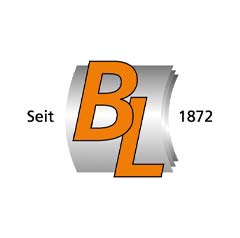
Blechwarenfabrik, produttore di lattine e contenitori metallici, ha aperto una nuova sede a Offheim (Germania) dove produce più di 100 milioni di contenitori all'anno. Il centro è composto da due magazzini automatici connessi alla produzione tramite Easy WMS di Mecalux che organizza la spedizione di materie prime.
Blechwarenfabrik: tradizione e innovazione
Blechwarenfabrik è uno dei principali produttori europei di lattine e contenitori metallici utilizzati in molti settori industriali (soprattutto per lo stoccaggio e la movimentazione di prodotti chimici).
- Anno di fondazione: 1872
- Team professionale: 500 persone
- Capacità produttiva: più di 100 milioni di contenitori metallici all’anno
- Stabilimenti di produzione: Germania, Danimarca, Russia e Polonia
SFIDE
|
SOLUZIONI
|
VANTAGGI
|
---|
Blechwarenfabrik, azienda leader in Europa nella produzione di contenitori metallici per prodotti chimici, ha automatizzato la sua logistica con l’obiettivo di affrontare l’incremento delle vendite.
A Offheim (Germania) la società ha un magazzino di 22.000 m2 dove tutti i movimenti della merce sono completamente automatizzati: veicoli a guida automatica (più conosciuti con l’acronimo AGV) connettono i due magazzini automatici con le linee di produzione in totale autonomia.
Prima l’azienda disponeva di due stabilimenti di produzione in Germania dove produceva tutti i contenitori metallici (lattine per bevande, conserve…) e la logistica era esternalizzata per mancanza di spazio di stoccaggio. "La materia prima veniva depositata nel magazzino principale e il prodotto finito, una volta uscito dalle linee di produzione, veniva portato in un magazzino a 5 km di distanza", spiega Christoph Weber, Responsabile tecnico della Blechwarenfabrik.
Decisa a limitare la dispersione logistica, a ridurre i costi e a centralizzare tutte le attività in un unico spazio altamente digitalizzato e sostenibile, la Blechwarenfabrik ha intrapreso il suo progetto più ambizioso fino ad oggi: la costruzione di una nuova sede a Offheim (Limburgo), dove si svolgeranno tutte le sue attività. Nelle installazioni moderne si trovano: gli uffici, 25 linee di produzione e un'area di stoccaggio. Lo stabilimento processa 22.000 tonnellate di acciaio per la produzione di oltre 100 milioni di contenitori metallici all'anno.
Il processo di centralizzazione della logistica e della produzione è stato portato avanti per gradi, poiché alcune fasi della produzione hanno dovuto essere riconfigurate e adattate al nuovo sito. I responsabili della Blechwarenfabrik hanno lavorato a stretto contatto con il team tecnico di Mecalux per trovare una soluzione personalizzata. “Un progetto su larga scala come il nostro non è facile da realizzare, perché abbiamo dovuto considerare molti dettagli. Con l'aiuto di Mecalux, il trasferimento di tutte le operazioni logistiche al nostro nuovo stabilimento è avvenuto in modo perfetto", afferma Weber.
La robotica per una maggiore efficienza e sostenibilità
Se c'è una cosa che la società aveva ben chiara è che voleva puntare sull'Industria 4.0, dotandosi della tecnologia per integrare automaticamente produzione e logistica. "Prima la gestione delle operazioni e della movimentazione delle merci era manuale. Gli operatori rifornivano la produzione con l'aiuto di carrelli elevatori. Inoltre, le nostre strutture erano divise in diversi stabilimenti, il che rendeva difficile la logistica interna", spiega il Responsabile tecnico.
Ora la produzione e lo stoccaggio sono concentrati sullo stesso piano con fino a quindici veicoli a guida automatica che spostano i prodotti da un punto all'altro del capannone con il minimo intervento dell'operatore. I robot ricevono istruzioni dal software di gestione magazzino (WMS) per sapere dove portare i prodotti. "Abbiamo automatizzato la gestione delle merci, dall'ingresso alla spedizione dei prodotti. In collaborazione con Mecalux, abbiamo costruito la fabbrica di imballaggi metallici più moderna d'Europa", sottolinea Weber.
Ridurre al minimo l'impatto ambientale dei processi produttivi e logistici è sempre stata una delle principali preoccupazioni di Blechwarenfabrik. Centralizzando tutti i processi in un unico spazio ed evitando così il trasferimento delle merci tra impianti di produzione e magazzini, l'azienda prevede di emettere 2.600 tonnellate di sostanze inquinanti in meno all'anno.
Lo stabilimento di Blechwarenfabrik dispone anche di un'area in cui i rifiuti metallici generati durante i vari processi industriali vengono raccolti per essere riciclati. Inoltre, sul tetto dello stabilimento sono stati installati 4.100 pannelli solari per generare l'energia utilizzata nel processo di produzione e stoccaggio.
Logistica e produzione: un collegamento efficiente con Easy WMS
Il nuovo stabilimento di Blechwarenfabrik è composto da due magazzini automatizzati: uno all'interno del capannone per le materie prime e l’altro nell’autoportante per i prodotti finiti. I magazzini autoportanti sono edifici costituiti dalle scaffalature stesse che sostengono il proprio peso, quello della pannellatura verticale e della copertura, nonché quello della merce. Ha inoltre implementato il software di gestione magazzino Easy WMS di Mecalux, un software che gestisce e ottimizza tutti i processi in entrambi i magazzini.
“L'integrazione della produzione e della logistica è stata una delle maggiori sfide di questo progetto. Abbiamo ottenuto questo risultato trasferendo progressivamente i processi produttivi nei nuovi impianti. Siamo stati in grado di analizzare e risolvere i problemi man mano che si presentavano", spiega Uwe Wonsack, Direttore operativo della Blechwarenfabrik.
Per unire in modo efficiente logistica e produzione, l'azienda utilizza il software Easy WMS. Il programma di Mecalux si collega all'ERP Infor di Blechwarenfabrike e al sistema di controllo della produzione (MES) per individuare gli articoli necessari alla produzione e organizzarne la distribuzione. "I programmi si sostengono a vicenda. Se cerchiamo informazioni sui prodotti, Easy WMS ci fornisce tutti i dettagli, la quantità disponibile o la posizione esatta", afferma Wonsack. L'ERP, a sua volta, si collega con altri software coinvolti nei processi produttivi, come quello che gestisce i robot di pallettizzazione utilizzati nella produzione, quello che raccoglie i dati sull'andamento delle operazioni in fabbrica o quello che organizza, controlla e monitora queste stesse operazioni.
Easy WMS comunica anche con il software di controllo dei veicoli AGV per organizzare il movimento delle merci tra i magazzini e la produzione. "Gli AGV alimentano automaticamente le linee di produzione. Quando Easy WMS riceve un ordine dalla produzione, il software ne organizza la preparazione in magazzino. Gli AGV prelevano i prodotti e li spostano sulla linea in cui sono richiesti. Il processo è trasparente, rapido ed efficace", sottolinea Wonsack.
Inoltre, il software di Mecalux organizza la gestione dei rifiuti nello stabilimento della Blechwarenfabrik. Quando si generano rifiuti nei processi produttivi, Easy WMS ne ordina l'invio all'area di riciclaggio.
Software di gestione magazzino: tracciabilità rigorosa
Easy WMS di Mecalux è uno strumento che fornisce una tracciabilità completa dei prodotti stoccati. Il programma traccia in modo esaustivo le merci, dall'arrivo delle materie prime fino alla spedizione dei prodotti finiti. Il collegamento tra logistica e produzione tramite Easy WMS ha portato a Blechwarenfabrik molti vantaggi:
- Visibilità e gestione dello stock in tempo reale. Easy WMS conosce lo stato e la posizione esatta delle referenze, sia delle materie prime che dei prodotti finiti.
- Supporto alla produzione just-in-time. Il software assicura che le materie prime siano inviate ai processi produttivi nella giusta quantità e al momento giusto.
- Gestione dell’anagrafica articoli e della distinta base. In ogni ordine di produzione vengono configurate le materie prime necessarie per la realizzazione dei prodotti.
- Miglioramento dei processi produttivi. Una buona organizzazione delle operazioni e un controllo preciso delle merci si traducono in una maggiore efficienza e agilità.
- Lavoro completamente digitalizzato. Gli operatori richiedono le materie prime di cui hanno bisogno tramite terminali a radiofrequenza o tablet.
“Il più grande cambiamento che abbiamo sperimentato con Easy WMS è stato il controllo delle scorte: ora possiamo sapere dove si trova ogni prodotto in ogni momento", aggiunge Wonsack. Il controllo delle scorte ha permesso a Blechwarenfabrik di organizzare meglio le merci, con un impatto anche sul regolare svolgimento delle operazioni. L'ordine è fondamentale per la società per garantire la fornitura just-in-time delle linee di produzione.
Supply chain totalmente automatica
Per Blechwarenfabrik era chiaro che l'automazione avrebbe contribuito a ridurre i costi e ad aumentare le prestazioni della supply chain. L'azienda ha ottimizzato e snellito i processi di stoccaggio, picking e spedizione della merce.
Trasloelevatori, trasportatori di pallet e veicoli a guida automatica (AGV) consentono un movimento permanente e controllato delle merci. Ogni giorno, 600 pallet con materie prime vengono inviati alle linee di produzione e, allo stesso tempo, 1.200 pallet con circa 500.000 lattine e contenitori metallici vengono prelevati dalle linee di produzione, stoccati e resi disponibili per la spedizione a centinaia di clienti della società in tutta Europa.
➤ Magazzino di materie prime
Alto 11 m e lungo 100 m, il magazzino automatizzato è composto da due corsie con scaffalature a singola profondità su entrambi i lati in grado di contenere 2.500 pallet con le lamiere utilizzate per la produzione delle lattine.
Il magazzino riceve in media 125.000 lamiere al giorno dai fornitori di Blechwarenfabrik. In collegamento permanente con il sistema MES (Manufacturing Execution System), la prima cosa che Easy WMS fa quando organizza la merce in arrivo è ordinare che i fogli siano collocati sul pallet giusto e nella posizione corretta. A seconda dell'articolo da produrre sulle linee di produzione, ogni lamiera deve essere collocata in una posizione o in un'altra sul pallet.
“Le merci sono organizzate secondo il criterio FIFO, cioè il primo pallet che entra è il primo che esce. In questo modo, evitiamo che gli articoli diventino obsoleti e possiamo garantire un flusso continuo di merce", spiega Wonsack.
Per assicurarsi che le linee di produzione abbiano la merce necessaria, Easy WMS controlla il numero di lamiere necessario per ogni ordine e la posizione richiesta. Se la quantità non è sufficiente, si selezionano altre lamiere dal magazzino e si portano alla macchina di tornitura dove viene indicato all'operatore come collocare le lamiere nella posizione corretta.
Seguendo le istruzioni di Easy WMS, gli AGV prelevano le lamiere in uno dei due punti di uscita del magazzino automatico e li trasferiscono automaticamente sulle scaffalature portapallet vicini alle linee di produzione.
Queste scaffalature fungono da buffer, stoccando temporaneamente le materie prime fino al loro utilizzo nelle linee di produzione. Una volta svuotata l’ubicazione, può essere rioccupata con un altro articolo per l'ordine di produzione successivo.
➤ Linee di produzione
Quando i processi produttivi iniziano, Easy WMS ordina ai robot AGV di inviare le materie prime e i semilavorati alle linee corrispondenti.
Uno dei semilavorati richiesti negli ordini di produzione sono i corpi delle lattine (chiamati bodies). Questi articoli non vengono stoccati nel magazzino automatico, ma vengono posizionati direttamente sulle scaffalature portapallet accanto alle linee di produzione. Easy WMS tiene traccia anche di questi prodotti e li ordina per inviarli alla produzione al momento giusto.
Dalla produzione, gli operatori possono comunicare con Easy WMS per ordinare, ad esempio, pallet vuoti, segnalare scorte difettose o restituire al magazzino materie prime in eccesso.
“Per noi è molto importante che gli operatori delle linee di produzione non debbano svolgere compiti secondari e possano concentrarsi sul loro lavoro principale. Tramite un terminale, gli operatori possono ordinare i prodotti da Easy WMS", aggiunge Wonsack.
Seguendo gli ordini di Easy WMS, gli AGV raccolgono anche i rifiuti e li portano automaticamente nell'area di riciclaggio.
➤ Magazzino per prodotti finiti
Con una capacità di 18.000 pallet, il magazzino automatico autoportante è alto 31 metri ed è composto da quattro corsie con scaffalature a doppia profondità su entrambi i lati.
Ogni ora arrivano circa 80 pallet dalle linee di produzione. Prima di entrare nel magazzino, questi prodotti passano attraverso una postazione di controllo dove si verifica che soddisfino i requisiti stabiliti per la loro ubicazione nelle scaffalature.
Successivamente, Easy WMS assegna quindi una posizione a ciascun prodotto. Il software incorpora regole e algoritmi per decidere la posizione migliore per ogni pallet, tenendo conto del suo riferimento e della sua rotazione.
Per quanto riguarda le spedizioni, l'ERP notifica a Easy WMS quali pallet devono essere distribuiti, e poi il WMS assegna una baia a ogni ordine in uscita. Ogni ora, 100 pallet escono da questo magazzino per andare all'area di picking o direttamente alle baie di carico. "I processi di spedizione si svolgono senza problemi", afferma Wonsack.
Nella parte anteriore del magazzino è stata allestita una postazione di picking. Qui gli ordini vengono prelevati secondo il criterio “prodotto verso uomo”, cioè gli operatori attendono di ricevere gli articoli necessari per ogni ordine. Gli operatori estraggono le scatole dai pallet provenienti dal magazzino e le posizionano su un altro pallet dove si raggruppano gli articoli che compongono l'ordine.
Gli operatori dispongono di uno schermo e di terminali a radiofrequenza per seguire passo dopo passo le istruzioni di Easy WMS. Con questi dispositivi, sono informati in ogni momento su quali prodotti rimuovere dai pallet e in quali ordini collocarli. Di conseguenza, Blechwarenfabrik ha ridotto al minimo la possibilità di errori.
I pallet inviati direttamente alla spedizione vengono etichettati e portati alla baia corrispondente. Al piano è stata allestita anche un'area di pre-carico dove i pallet vengono raggruppati e classificati in base all'ordine a cui corrispondono o al percorso di trasporto, in modo da velocizzarne il carico sul camion di distribuzione.
Industria 4.0 per l’efficienza e la sostenibilità
Blechwarenfabrik ha assicurato e incrementato il proprio tasso di crescita grazie alla tecnologia. L'azienda è passata all'Industria 4.0 per controllare al meglio i processi e servire i clienti in modo più efficiente. Con l'aiuto dell'automazione, la società non solo ha aumentato il proprio rendimento, arrivando a produrre più di 100 milioni di confezioni all'anno, ma ha anche beneficiato di una catena di approvvigionamento più sostenibile.
Grazie alle soluzioni automatizzate di Mecalux e alla gestione di Easy WMS, l'azienda dispone di una supply chain interconnessa. Tutti i processi sono coordinati dal software con un unico scopo: servire le linee di produzione al momento giusto. Digitalizzazione e automazione sono una combinazione vincente per Blechwarenfabrik e contribuiranno senza dubbio alla crescita futura della società.
Quando abbiamo aperto il nostro nuovo stabilimento di Offheim (Limburgo), era chiaro che dovevamo potenziare l'automazione. Con la tecnologia del nostro partner Mecalux, la nostra catena di fornitura ha fatto salti da gigante.
Galleria
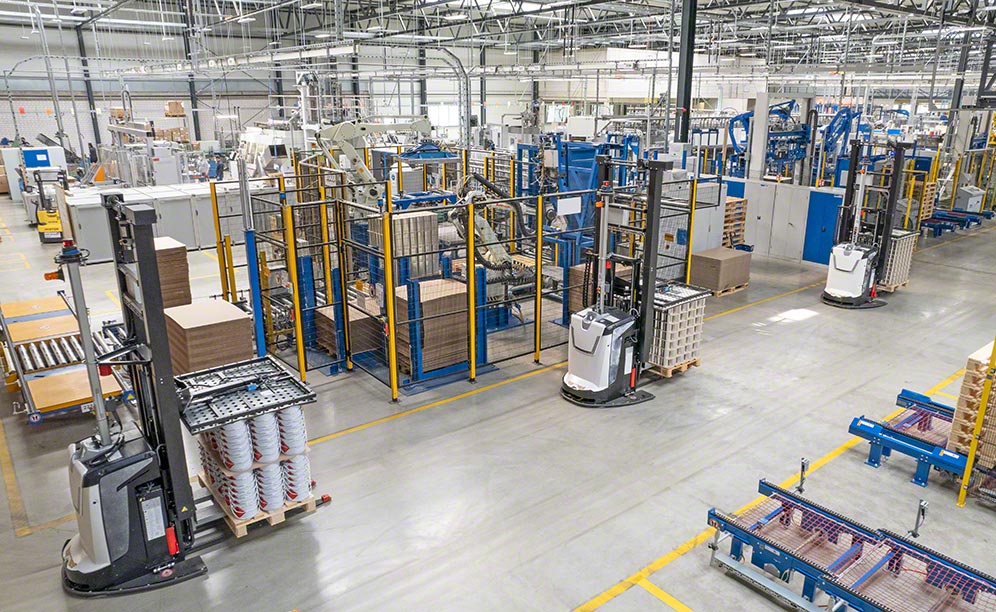
Magazzino automatico di materie prime di Blechwarenfabrik a Limburgo (Germania)
Consultate un esperto