Il pavimento industriale è un elemento chiave del magazzino che deve garantire elevate prestazioni in termini di resistenza alle sollecitazioni. Una buona pavimentazione si sceglie in base ai carichi che deve sopportare o al tipo di rivestimento che si applicherà. In questo articolo analizzeremo in profondità caratteristiche e aspetti rilevanti che riguardano la pavimentazione industriale, concentrandoci in particolare sull'importanza della composizione e del substrato, descrivendo il processo di piallatura, lo strato di finitura e le tolleranze.
Pavimentazione e tipi di carichi
Il pavimento di un magazzino è associato al concetto di carico. Esistono due tipi di carico: statico e dinamico, ognuno caratterizzato dal tipo di intensità e dai livelli di pressione e concentrazione (in tonnellate) sulle scaffalature.
I carichi statici
Sono quelli che si generano sotto i montanti delle scaffalature. Sono carichi di tipo specifico, di grande intensità, concentrati in una piccolissima superficie di pavimento ed equamente suddivisi sull’intera platea di fondazione del magazzino. Questi carichi preoccupano maggiormenti i costruttori, poiché parliamo di livelli di 7/8 tonnellate concentrati in uno spazio ridotto - quello della sezione del profilo del montante - di soli 80 o 100 cm2.
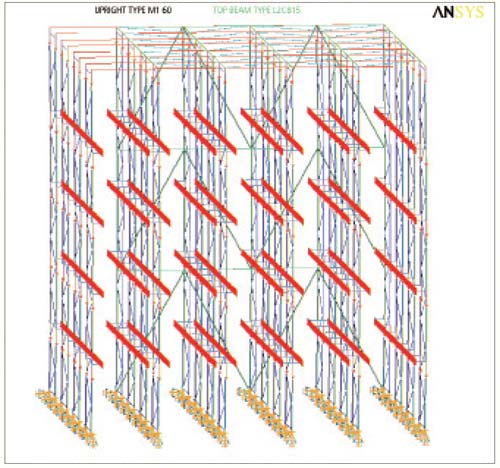
Lo studio della carica nominale che devono sopportare le scaffalature.
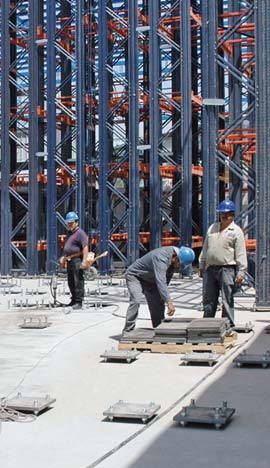
Analisi della pavimentazione durante la fase di costruzione.
I carichi dinamici
I carichi dinamici sono prodotti dai mezzi di sollevamento che circolano lungo corridoi stretti. Si tratta sempre di quantità di carico importanti che variano in base al tipo di macchina utilizzata. Nel caso più estremo del trasloelevatore, il peso può raggiungere le 18 t ed essere concentrato su una superficie minima di pavimento, quella dell’impronta della ruota di carico. Tale effetto si riduce tuttavia al minimo, dal momento che viene distribuito sull’intero binario guida su cui si muove la macchina.
Altre tipologie di mezzi di sollevamento producono i carichi più pesanti quando sono fermi. Nel caso del carrello trilaterale, invece, l'effetto di carico sul pavimento si verifica in fase di deposito o di prelievo alla massima altezza e con le forche estese lateralmente. In quel momento, la pressione esercitata sulle ruote di carico raggiunge valori talmente alti che possono superare i limiti di resistenza della pavimentazione, delle ruote stesse e dei relativi cuscinetti. Tale sforzo viene trasmesso direttamente ai lati dei corridoi.
Il carrello elevatore, dal canto suo, produce la massima pressione a terra quando è scarico, rilasciando l'effetto del contrappeso sulle ruote posteriori. Quando il carrello è carico si verifica un livellamento del carico sulla parte anteriore (secondo il principio della leva) e, sebbene il peso complessivo aumenti, viene distribuito sull’intera superficie della macchina. In questo caso, anche il carico viene sopportato da una superficie ridotta, quella dell’impronta degli pneumatici.
Gli elementi del pavimento industriale sicuro
La funzione di un pavimento industriale (e delle relative fondamenta) consiste nel sopportare e trasferire i carichi appena descritti dalla superficie della pavimentazione verso il basso, fino a raggiungere il livello del sottosuolo.
Questa proprietà è applicabile sia ai carichi dinamici derivanti dalle macchine in movimento, sia a quelli statici generati dai montanti delle scaffalature. Pertanto il pavimento industriale adeguato è ingrado di assicurare la durezza e la stabilità necessarie per svolgere tale funzione.
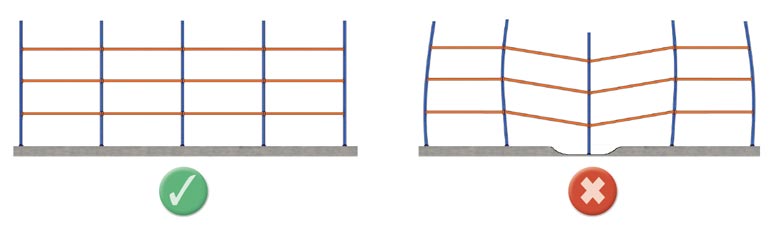
Finitura della superficie
La finitura della superficie deve essere correttamente livellata entro i margini e le tolleranze necessari per l’impiego all'interno del magazzino sia di macchinari specifici sia dei sistemi di stoccaggio. Il conseguimento di tali obiettivi e livelli qualitativi è a carico di progettisti e costruttori.
L’importanza del substrato
Prima di iniziare la posa di un pavimento industriale all'interno di un impianto, è indispensabile esaminare il substrato o lo strato solido su cui poggerà. Il substrato è variabile e può presentare grandi differenze anche tra punti vicini tra loro o addirittura occupanti il medesimo spazio, dal momento che le variazioni tra un punto e l’altro dello stesso edificio possono essere davvero significative.
I parametri principali da tenere in considerazione sono:
- La resistenza alla compressione.
- La tendenza allo scivolamento.
- La possibilità di assorbimento dell’acqua.
Per conoscerne i valori si eseguono una serie di analisi sul posto:
- Bisogna assicurarsi che il substrato del magazzino sia in grado di sopportare in toto il carico da sistemare sulla relativa pavimentazione. In base ai risultati ottenuti dagli opportuni esami, si sceglieranno il luogo e l’area su cui costruire la struttura.
- Le caratteristiche di questa parte del terreno influiscono in maniera decisiva sulle fondamenta. Per la loro realizzazione, è possibile utilizzare dei semplici cuscinetti di supporto o delle sponde più o meno larghe fino a ottenere, nei casi più estremi, una completa platea di fondazione.
- A volte le caratteristiche del substrato obbligano a variare la posizione dei montanti delle scaffalature, in modo tale che coincidano con i punti in grado di offrire le opportune garanzie.
Composizione della pavimentazione
Il pavimento industriale del magazzino è solitamente costituito da uno strato di fondazione di materiale agglomerato ben compattato per sopportare il carico. Tale strato è costituito da qualsiasi tipo di materiale, sia esso naturale o di riempimento. Sullo strato di fondazione si posa una lastra di calcestruzzo che dovrà sopportare la pressione della struttura.
Composizione pavimentazione
Le lastre di calcestruzzo presentano un’elevata resistenza alla compressione, ma una scarsa resistenza alla tensione. Durante il processo di asciugatura, il calcestruzzo subisce delle contrazioni, mentre ciò non avviene con lo strato di fondazione. Tali contrazioni determinano tensioni sulle lastre e ciò potrebbe comportare eventuali rotture e incurvamenti. Per ridurre tali problemi, è necessario assicurarsi che la superficie del substrato su cui poggia la lastra sia completamente levigata e liscia.
Una volta verificato questo aspetto, si inserisce una specie di membrana o pellicola tra lo strato di fondazione e il substrato per ridurre la frizione tra i due. Durante il processo di asciugatura, tale pellicola consente alla lastra di muoversi in modo indipendente e funge da barriera contro l’umidità, necessaria al fine di limitare la dispersione di acqua dal calcestruzzo e ottenere una migliore asciugatura.
Un’altra misura volta a ridurre il problema delle potenziali rotture e il frequente imbarcamento consiste nell’installare una leggera rete metallica di rinforzo che rimanga vicina alla superficie. Si tratta di una prassi piuttosto comune che consente di costruire lastre di lunghezza maggiore con meno giunti di dilatazione.
È inoltre possibile inserire un rinforzo a base di barre di acciaio al fine di aumentare la resistenza dello strato asciutto, nonostante le inevitabili contrazioni e gli spostamenti del calcestruzzo in tale fase. Che si inserisca o meno tale rinforzo, è inevitabile che possano comparire crepe nelle lastre asciugate, anche quando si presta la massima attenzione in fase di costruzione.
Nel caso in cui tali crepe si verifichino in modo casuale e non controllato, l’impossibilità di eseguire un adeguato riempimento, vista l’irregolarità delle medesime, provoca sempre problemi di fluttuazione dei carichi.
È frequente indurre la formazione di crepe affinché tali aperture compaiano in luoghi specifici da poter osservare e tenere sotto controllo. Ciò avviene segando la lastra lungo una determinata porzione, con un taglio di profondità pari a un quarto o un terzo dello spessore dello strato. In questo modo la rottura si sviluppa in quella posizione e non in un’altra e può essere agevolmente colmata.
Giunzioni nella pavimentazione
Le giunzioni nelle pavimentazioni delle strutture possono avere più origini e derivare da porzioni individuali lungo la pavimentazione o dalla costruzione stessa (verificandosi tra la fine di una giornata di lavoro e l’inizio della seguente). Possono essere state create per evitare o fiancheggiare colonne o muri.
Indipendentemente dalla loro origine, possono rappresentare un grave problema dal momento che subiscono l'erosione causata del costante passaggio dei carrelli. Le giunzioni devono legarsi o fissarsi alla struttura dello strato di fondazione per evitare il trasferimento dei movimenti al di sotto delle lastre adiacenti.
Nei giunti di dilatazione, i perni devono incassarsi e sistemarsi in maniera allineata. Tali perni devono avere un’estremità di scorrimento libera, dotata di un manicotto di plastica annegato in una delle lastre. I giunti di dilatazione, inoltre, devono avere una larghezza proporzionale allo spessore della lastra, che non deve tuttavia mai superare i 10 mm.
Sebbene possano essere applicati in qualsiasi punto, è sempre bene evitare i luoghi nei quali si presentino costantemente carichi importanti, ovvero lontano dai montanti delle scaffalature.
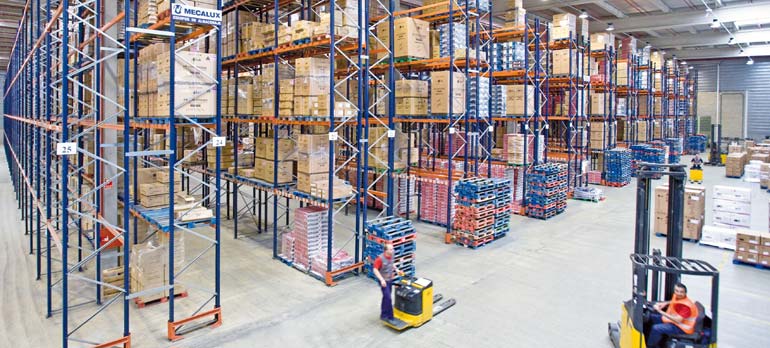
Magazzino per azienda che si occupa di elettronica di consumo. Fonte: Mecalux.
Lo strato di finitura
Sullo strato di fondazione e sulla lastra si installa un terzo strato di finitura che costituisce la vera a propria superficie di lavoro. Solitamente è costituito da una miscela di cemento granulare di 50 mm circa di spessore. Il cemento granulato viene applicato sulla lastra umida di calcestruzzo industriale, formando un blocco ed ereditandone le giunzioni.
La morbidezza, la resistenza e le qualità per la lavorazione di tale materiale conferiscono alla pavimentazione la capacità di sopportare le condizioni d’uso delle macchine nel magazzino.
A questo punto si pone una questione: lo strato di finitura deve essere effettuato assieme alla lastra e quindi essere soggetto alle stesse problematiche e ai medesimi trattamenti, in particolare per quanto riguarda le giunzioni? Oppure deve essere installata in maniera assolutamente indipendente?
Tale strato può essere applicato in maniera del tutto indipendente e separatamente su una lastra asciutta, ma è necessario che lo spessore di quest’ultima sia di almeno 125 mm. In tal caso si predispone un nuovo strato di calcestruzzo con i medesimi problemi di fragilità e imbarcamento della lastra principale, dal momento che la superficie di finitura si comporterà e si contrarrà in forma indipendente.
Per evitare ciò, è necessario inserire una nuova pellicola o membrana divisoria, in modo tale da formare un sottilissimo strato che non presenti giunzioni apprezzabili. Mediante l’aggiunta di prodotti bituminosi o di una vasta gamma di copolimeri, è possibile ottenere miscele di calcestruzzo di incredibile finezza.
Se si utilizzano resine sintetiche, è possibile ottenere uno strato di soli 3 mm, presupponendo una pavimentazione di ottima finitura. D’altro lato, se si desidera ottenere una superficie più comoda è possibile usare resine dotate di maggiore resilienza, ovvero di maggiore capacità elastica per assorbire la deformazione e recuperare quando si smette di esercitare pressione.
Tuttavia, è necessario tenere conto del fatto che certi strati ottenuti mediante miscele speciali possono non essere stabili o non avere qualità granulari complete, come ad esempio nel caso di utilizzo di resine non adeguate a correggere difetti dello strato superiore. Oltre a risultare instabili, queste miscele presentano costi eccessivi.
I pavimenti per magazzini richiedono quindi un’elaborazione molto accurata e una manutenzione preventiva per essere utilizzati. In questo modo si potranno evitare e correggere le anomalie e lacerazioni che producono le ruote dei carrelli quando circolano e attraversano le giunzioni. Nei magazzini automatici non sono necessari strati di finitura così consistenti, poiché in essi non circolano i carrelli.
Piallatura per una superficie liscia
Spiegati i concetti fondamentali e gli elementi che compongono una pavimentazione, è il momento di esaminarne la costruzione. Dopo aver preparato la cementazione e realizzato il livellamento dello strato di fondazione, è necessario decidere il tipo di spalla da utilizzare e il metodo di spianamento del terreno, che differiranno in funzione dell’intenzione di realizzare una pavimentazione a basso o alto indice di tolleranza.
Il metodo di piallatura della pavimentazione si basa sull’uso di una livellatrice, utilizzata da due operai che si dedicano a far sì che il calcestruzzo venga perfettamente assorbito dalla spalla. Nel frattempo, altri due operai si muovono lungo la superficie muniti di un rullo compattatore.
Il rullo compattatore agevola la lisciatura della superficie, ma non completa il lavoro. Il calcestruzzo non deve essere manipolato eccessivamente, per evitare che i granuli pesanti e gli additivi cadano verso la parte inferiore della pavimentazione o dello strato.
Per ottenere tolleranze strette nella superficie di finitura, senza ricorrere a un lavoro straordinario, è necessario che il calcestruzzo non trovi grandi dislivelli o buche nello strato di fondazione.
È necessario prestare particolare attenzione pertanto alla piallatura della pavimentazione affinché abbia un alto grado di livellamento altrimenti, ad ogni fase della costruzione, diventerà progressivamente più difficile ottenere le tolleranze richieste, su questo aspetto influisce anche la spalla scelta.
Per una pavimentazione con una tolleranza relativamente bassa, se ne può usare una in legno, ma quando sono richieste alte tolleranze è necessario impiegare, per lo meno, spalle di metallo.
Il motivo è che la precisione della rettilineità e della livellazione dipendono dalla spalla utilizzata. Quanto maggiore è il grado di affidabilità della pavimentazione, tanto migliori saranno i risultati.
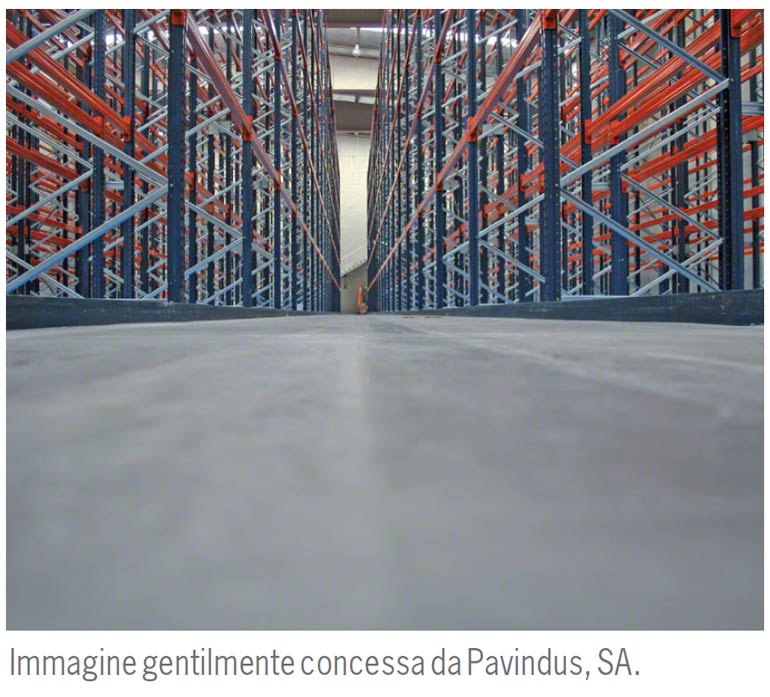
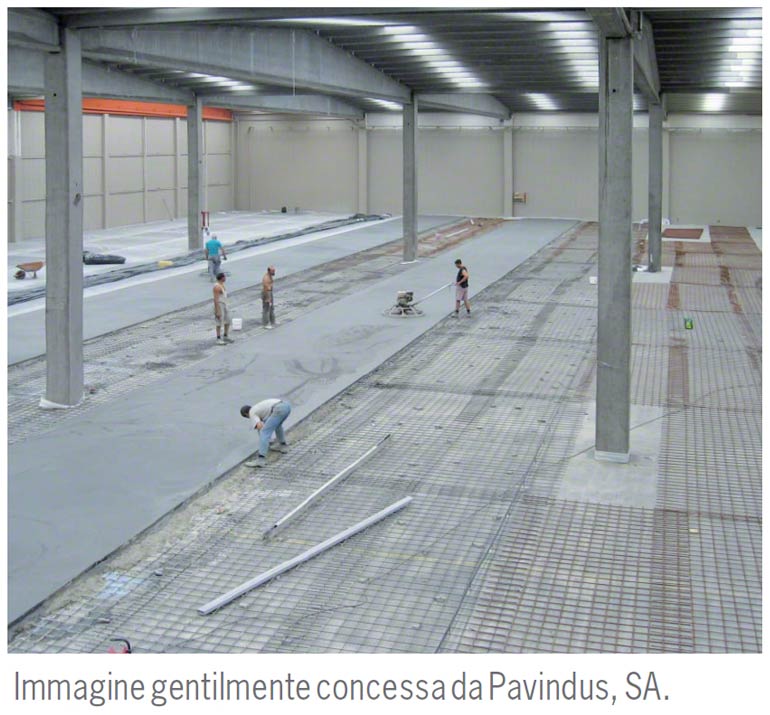
Fattore umano: l'abilità degli operatori
Una pavimentazione adeguata si ottiene anche grazie al fattore umano ovvero all'abilità degli operatori nel manovrare i mezzi meccanici di compattazione e finitura. Un sistema abituale per l’esecuzione di una pavimentazione tradizionale consiste nello spianamento di strisce di calcestruzzo che sono completate man mano che vengono costruite.
Questo sistema può presentare due problemi nel caso di pavimentazioni con una tolleranza alta:
- Accesso disordinato alle zone di riempimento durante il processo di verifica.
- Difficoltà fisica a realizzare strisce larghe, potrebbe essere necessario utilizzare strisce strette e lunghe.
Attualmente si ottengono strisce comprese tra i 9 e i 15 m in locali con pavimenti con un indice di tolleranza molto alto. A tale scopo, è necessario disporre di personale altamente specializzato e utilizzare livellatrici progettate specificamente per questo lavoro. Il metodo più adoperato consiste nel realizzare strisce alterne una dietro l’altra. Il resto viene completato successivamente, dopo un breve periodo di riposo.
Resistenza, porosità e durata delle pavimentazioni
Oltre alle caratteristiche costruttive già illustrate in precedenza, le pavimentazioni dei magazzini devono contare su altre capacità che le rendano idonee all’uso specifico al quale sono destinate.
Il pavimento industriale deve:
- Resistere alle abrasioni, questione prevista dalla normativa UNI EN 101 che stabilisce una scala conosciuta con il nome di MOHS, che va da 0 a 10.
- Resistere alla compressione e sopportare carichi superiori ai 500 kg/cm2, nelle aree generali. In base alle macchine utilizzate, è possibile che debbano resistere fino a 800 kg/ cm2 nelle vie di transito. Per quanto riguarda i requisiti della resistenza alla flessotrazione, in genere sono intorno ai 150 e i 250 kg/cm2.
- Sopportare l'azione di elementi quali oli, grassi e idrocarburi, dato che anche se tali materiali non vengono stoccati nella struttura vengono ugualmente impiegati nei carrelli e possono inevitabilmente produrre macchie sul suolo. Per quanto riguarda la porosità ammissibile, è necessario che sia molto bassa, con valori inferiori al 3%.
- Formare un blocco unico con la base di supporto al fine di evitare slittamenti e movimenti verso il basso che possano dar luogo a buche sulla superficie.
- Essere durature e resistenti all’usura, anche se è inevitabile che con il tempo si formino delle traccie di ruote prodotte dal continuo passaggio delle macchine e provocati del loro enorme peso. Le traccie delle ruote possono arrivare a essere molto profonde e provocare anomalie all’impianto, con il conseguente rischio implicito.
Considerazioni finali
Affidarsi a un'azienda specializzata nella realizzazione di pavimentazioni per il magazzino è fondamentale, in quanto userà la propria esperienza per adattare le esigenze economiche (del cliente) a quelle pratiche (dei carrelli che si muoveranno in corsie di lavoro strette).
Il pavimento industriale, oltre ad essere la superficie su cui tutti, operatori e macchine, svolgeranno il proprio lavoro, è anche la base del magazzino. Gli investimenti destinati alla realizzazione di un impianto di alto valore e rendimento potrebbero andare in fumo se non si dispone della giusta base su cui operare.
Per maggiori informazioni, approfondimenti o consulenze, i nostri esperti sono sempre a vostra disposizione.