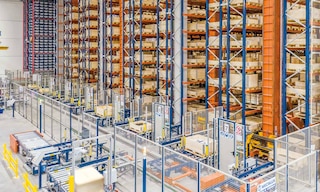
I PLC nella logistica, primo passo verso l’automatizzazione del magazzino
La crescita dei Controllori Logici Programmabili, PLC (Programmable Logic Controller, in inglese) nella logistica va di pari passo con l’automatizzazione dei magazzini e dei centri di produzione. Si tratta di dispositivi la cui funzione è quella di eseguire un programma di automazione in ambienti logistici e industriali.
In altre parole, sono quei dispositivi incaricati di processare le indicazioni ed eseguire i movimenti programmati affinché l’installazione automatica funzioni correttamente.
Cos’è un PLC o Controllore Logico Programmabile?
Il Controllore Logico Programmabile è la pietra miliare dell’automazione industriale. Molti sistemi automatici per magazzini si affidano a un controller industriale PLC che semplifica l’automatizzazione dei movimenti. Nel contesto della robotica è importante non confondere la sigla PLC con Power Line Communications, cioè, la tecnologia che permette lo scambio di informazioni mediante linee ad alta tensione.
Il funzionamento del PLC è il seguente: il processore comunica con il software di livello superiore, che processa l’informazione ricevuta dal software di gestione magazzino ed esegue le attività in funzione di regole pre-programmate. Questo tipo di microprocessori, in genere più robusti di un PC, lavorano in tempo reale: ricevono le informazioni dai canali di entrata ed eseguono i movimenti della macchina dai canali di uscita.
Componenti di un PLC
I PLC hanno una struttura di base, simile a quella di un computer, formato da:
- CPU: unità centrale di elaborazione che interpreta ogni istruzione programmata.
- Alimentatore: componente che fornisce energia alla CPU e al resto degli elementi del PLC.
- Memoria: spazio disponibile del processore dove vengono conservate tutte le informazioni necessarie per eseguire l’attività di controllo.
- Canali di ingresso e uscita: moduli analogici e digitali che garantiscono il successo nell’esecuzione del PLC. I canali di entrata elaborano le informazioni del software superiore, mentre quelli di uscita permettono il collegamento fisico tra il computer e il robot da muovere.
- Unità di programmazione: insieme di hardware e software che permette al PLC di interpretare, in uno o nell’altro linguaggio di programmazione, le istruzioni che riceve da un altro programma.
Come curiosità, questi robot vengono programmati per mezzo di linguaggi come il Ladder, molto popolari in questi impianti, basati su diagrammi di contatto e schemi di controllo classici. In questi ultimi anni si sono incorporati i linguaggi IEC che semplificano l’uso di uno stesso programma nel PLC di differenti produttori.
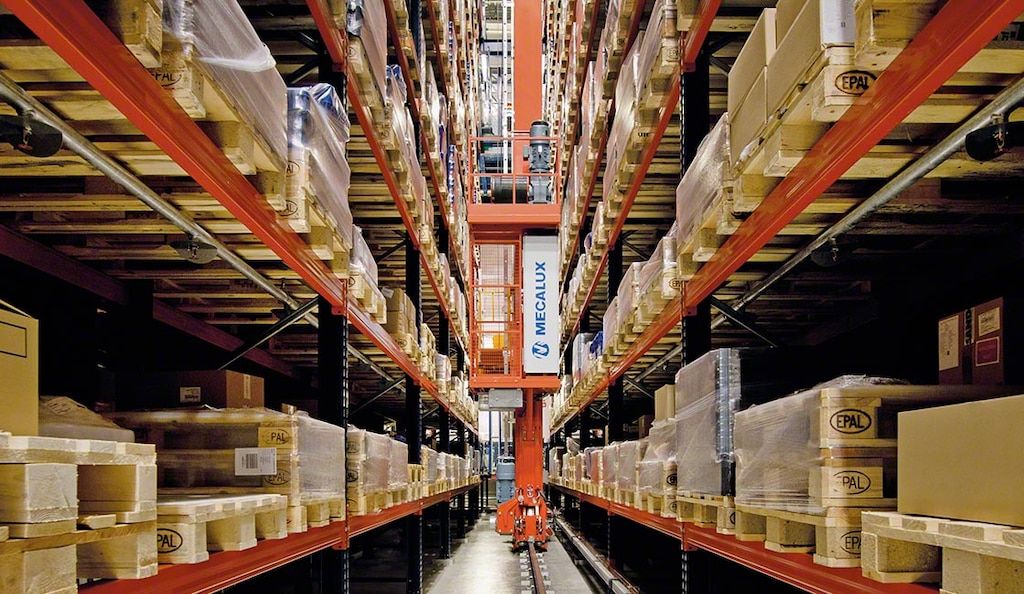
Differenze tra PC e PLC
È facile confondere i Controllori Logici Programmabili con i differenti PC di controllo che esistono in qualunque postazione di lavoro di un magazzino, poiché tutti e due possono controllare i movimenti di un robot industriale a partire dalle informazioni ricevute da un software di livello superiore. Entrambi gli hardware, inoltre, possiedono una struttura simile: una CPU, un insieme di segnali di entrata, di uscita e memoria.
Tuttavia, i Programmable Logic Controllers non dispongono di un sistema operativo, il che impedisce che possano utilizzare una base dati. Al contrario, un PC funziona con un SO, dove viene installato un software come Galileo (utilizzato da Mecalux nelle sue installazioni), che ricava informazioni sullo stato dell’installazione e riceve istruzioni per attivare il movimento dei sistemi automatizzati.
Ad ogni modo, un PLC comporta numerosi vantaggi rispetto a un PC industriale: offre la possibilità di incorporare programmi di sicurezza con entrate e uscite più sicure, ideali per quei processi che non ammettono margine d’errore.
Oltre a questo, i Controllori Logici Programmabili, nella logistica e nella produzione, risultano essere uno strumento perfetto, in quanto sono più robusti e sono stati progettati per disporre di protezioni in ambienti complessi (con vibrazioni ad alta frequenza, corrosione o cambi di temperatura).
Mecalux utilizza una combinazione di PC e PLC nelle sue installazioni per sfruttare i benefici offerti da entrambi.
Funzioni e applicazioni dei PLC nel magazzino
I PLC rappresentano il primo passo per l’automatizzazione di un magazzino, poiché, oggigiorno, si usano in qualsiasi luogo dove sia presente un sistema robotizzato. Questi processori robusti lavorano come un computer da tavolo, salvo che le loro funzioni sono particolarmente adatte per gli ambienti industriali. Perché? I sistemi operativi che usano i computer sono meno stabili di quelli dei PLC, oltre a non essere stati progettati specificamente per resistere alle condizioni di lavoro di industrie e magazzini.
I PLC, di solito, vengono installati nei processi industriali che richiedono poco spazio, un controllo dei processi o che utilizzano sequenze multiple per effettuare differenti attività. Grazie alla loro grande resistenza sono strumenti idonei per eseguire i movimenti automatizzati di un magazzino: dai robot pick and place delle postazioni di picking nell’industria automotive fino ai sistemi automatizzati di stoccaggio della merce in settori quali il chimico o il farmaceutico. Di fatto, una grande maggioranza dei sistemi automatici di stoccaggio o trasporto, come i miniload o i sistemi di trasportato per contenitori, sono controllati dai PLC.
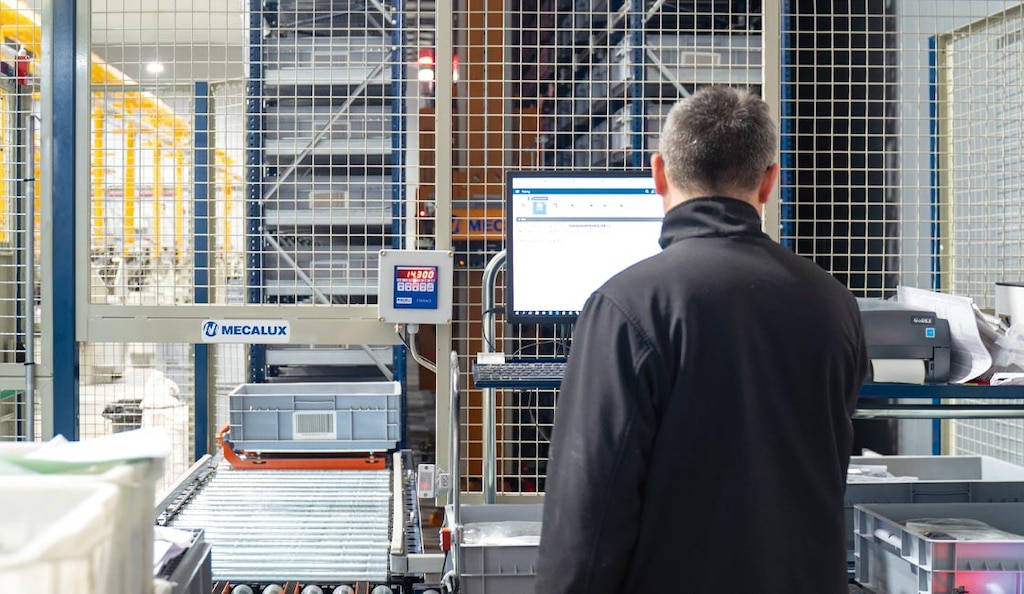
La relazione tra PLC, WCS e WMS
Un PLC (Programmable Logic Controller) è un hardware dove viene ubicato un programma specializzato per interpretare le informazioni ricevute da un software di livello superiore e fare eseguire i movimenti ai sistemi automatizzati.
Un WCS (warehouse control system) è il software di livello superiore che invia i dati al PLC o al PC industriale affinché questo si occupi di muovere la macchina. Questo programma informatico comanda gli elementi che controllano l’uscita della merce e la gestione delle ubicazioni. Effettua un controllo dal percorso dei trasloelevatori per pallet all’area di picking ubicata nella testata, passando per qualunque elemento automatizzato.
Tuttavia, esiste anche un terzo programma logistico che lavora come “cervello del magazzino”: indica al WCS, tra le altre variabili, gli ordini da inviare ai PLC in funzione dei criteri di ubicazione, delle strategie di picking o delle rotte parametrizzabili delle spedizioni. Questo software è il sistema di gestione magazzino (WMS).
PLC: uno dei pilastri dell’automazione industriale
Sia per mezzo di PLC che tramite un PC con un software integrato, la coordinazione tra i differenti sistemi automatizzati è fondamentale affinché un magazzino sia efficiente e produttivo. A questo bisogna aggiungere che l’automatizzazione industriale è sempre più una realtà dei centri logistici: secondo l’ultimo studio della società di consulenza LogisticsIQ, infatti, si prevede che il volume di affari di questo settore superi i 30.000 milioni di dollari nel 2026.
In questo contesto, il corretto funzionamento del magazzino automatico dipende da un sistema che assicuri la sincronizzazione tra tutti i sistemi automatizzati, promuovendo la sicurezza, la produttività e, soprattutto, l’efficienza dell’installazione.
Vuoi incrementare il rendimento della tua logistica? Contattaci subito, un nostro esperto ti consiglierà la soluzione più adatta alla tua attività. Il nostro staff di professionisti progetterà e implementerà un magazzino adatto al tuo tipo di prodotto, alla tua installazione e alle tue esigenze.