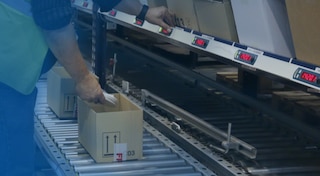
Il metodo Poka-Yoke in 5 esempi
Poka-Yoke è una tecnica di miglioramento continuo che ha due obiettivi fondamentali: evitare errori involontari durante i processi di produzione e logistica e correggere le inefficienze qualora si verifichino.
Attualmente, l’omnicanalità ha costretto le aziende a preparare e consegnare ogni giorno un elevato numero di ordini in tempi brevissimi. In questo scenario, i Responsabili del magazzino si sforzano di eliminare eventuali errori che comportano ritardi e perdita di fiducia dei clienti.
In che modo il metodo Poka-Yoke contribuisce a eliminare gli errori nel picking? In questo articolo, vedremo esattamente di cosa si tratta e spiegheremo come applicarlo.
Che cos’è il Poka-Yoke?
Creato nella fabbrica Toyota in Giappone nel 1960, il metodo Poka-Yoke significa letteralmente “a prova di errore”. Si tratta di una tecnica di miglioramento continuo che mira a evitare errori nei processi produttivi e logistici.
Il Poka-Yoke comprende le strategie che perfezionano e ottimizzano le procedure di un magazzino o di uno stabilimento di produzione come, ad esempio le 5S del metodo Kaizen.
Si può applicare anche agli oggetti progettati allo scopo di prevenire gli errori umani, come i cavi USB, utilizzati per trasmettere dati e caricare dispositivi, che se inseriti nella porta dal lato sbagliato, non funzionano.
L’ingegnere Shigeo Shingo sviluppò questa filosofia di lavoro allo scopo di eliminare le inefficienze durante i processi di produzione e la sua implementazione diede ottimi risultati. Un successo ottenuto applicando pratiche di semplificazione del lavoro degli operatori che in questo modo riducono al minimo le distrazioni affinché possano concentrarsi sulle attività da svolgere.
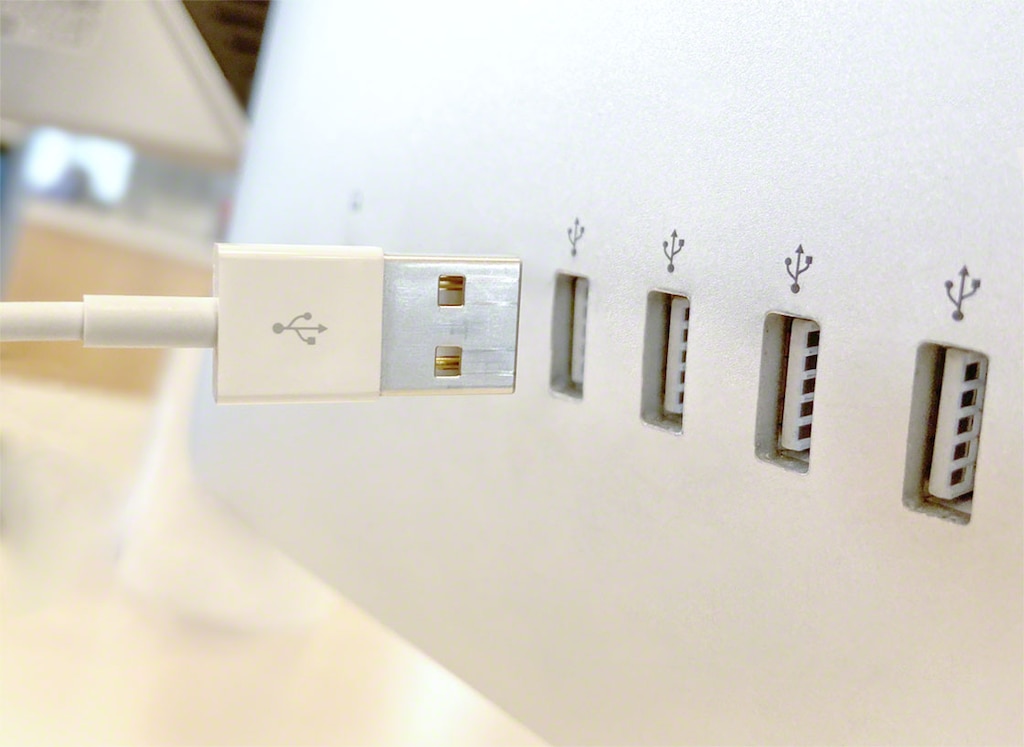
Come si applica il Poka-Yoke?
La domanda principale è: come adottare il Poka-Yoke, ad esempio, in uno stabilimento di produzione o in un magazzino? Prima di tutto, bisogna identificare e analizzare i singoli processi. Nell’analisi si studia come si sviluppa ciascun ciclo operativo, evidenziando gli eventuali errori che possono verificarsi.
Successivamente, si sceglie la strategia Poka-Yoke idonea, ossia si propone una soluzione che riduca al minimo o prevenga eventuali errori. Si suppone altresì che vi siano errori inevitabili e in quest’ottica si progetta un sistema di rilevamento e reazione che ne riduca l’impatto.
Infine, si monitora il ciclo operativo al fine di verificare l’efficacia del Poka-Yoke e della sua implementazione.
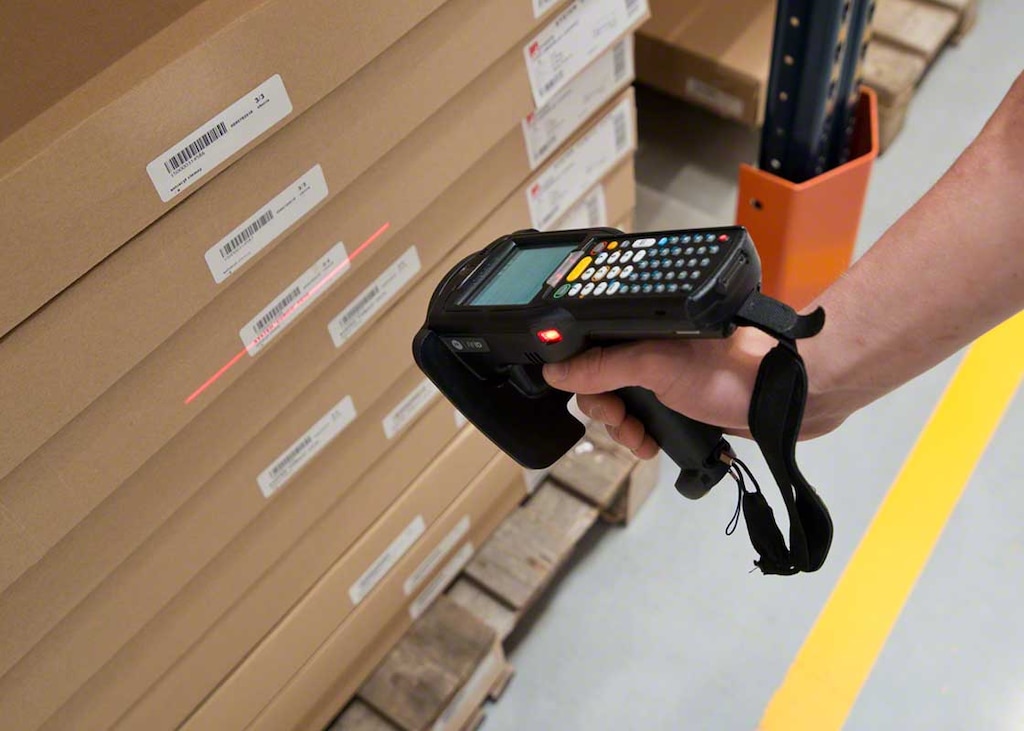
Tipi di Poka-Yoke
Il Poka-Yoke si può classificare in quattro tipi:
- Sequenziale. Alla base c’è il rispetto dell’ordine o della sequenza di un processo. In caso contrario, è impossibile concludere l’attività e quindi passare al processo successivo.
- Informativo. Informazioni chiare, semplici e dirette consentono agli operatori di svolgere i vari cicli operativi senza commettere errori.
- Raggruppato. Prevede la preparazione dei kit e di tutti i materiali e le parti necessarie al completamento di un ciclo operativo. In questo modo, gli operatori hanno a portata di mano i materiali necessari per lavorare e non perdono tempo per andarli a cercare.
- Fisico. Si tratta di variazioni nella fruibilità di alcuni dispositivi con l’intento di evitare errori. Ad esempio, le lavatrici o i forni a microonde utilizzati in casa non si avviano fino a quando lo sportello non è opportunamente chiuso o non è stata rispettata una determinata sequenza (selezione della temperatura, della durata, del programma ecc.)
Tutte queste pratiche hanno lo scopo di eliminare gli errori nelle attività ripetitive o in quei processi in cui gli operatori possono commettere errori per mancanza di conoscenza o per una svista. Come risultato, gli operatori possono dedicarsi al proprio lavoro senza sprecare tempo in verifiche o correzioni di inefficienze.
Cinque esempi di Poka-Yoke incentrati sulla logistica
In realtà, non esistono regole fisse per la creazione di un Poka-Yoke. Le pratiche applicate agli oggetti utilizzati per eliminare errori dipenderanno dall’ingegnosità degli individui coinvolti in ciascun processo.
Di seguito, vedremo attraverso alcuni esempi quali pratiche di Poka-Yoke si impiegano più spesso in un magazzino. Nel settore logistico, il Poka-Yoke rientra nella cosiddetta Lean logistics, ossia una modalità di lavoro volta a potenziare quei processi logistici che aggiungono valore con l’obiettivo di ridurre i costi.
Esempio 1: Poka-Yoke sequenziale con un software gestionale
Un software di gestione magazzini come Easy WMS di Mecalux ottimizza i cicli operativi e coordina gli operatori affinché svolgano la loro attività in tutta rapidità ed efficienza.
Il WMS funge da Poka-Yoke sequenziale poiché gli operatori, attraverso i terminali a radiofrequenza, seguono una dopo l’altra le indicazioni. Il software indica la successione delle attività e gli operatori devono confermare il completamento di ciascuna azione in attesa di ricevere ulteriori ordini.
Esempio 2: Poka-Yoke informativo con indicatori pick-to-light
La preparazione degli ordini è uno dei cicli operativi del magazzino a maggior rischio di errori. La stanchezza fisica degli operatori, la somiglianza tra i prodotti o la similarità tra le scaffalature possono causare confusione (ordini con articoli mancanti, sbagliati o in numero inesatto ecc.)
Una soluzione per evitare errori nel picking sono i dispositivi luminosi pick-to-light. Questa tecnologia, che rientra nel Poka-Yoke informativo, indica in modo visivo ed evidente la quantità e la tipologia di prodotti da prelevare. L’obiettivo è condurre l’operatore verso un approccio "zero errori".
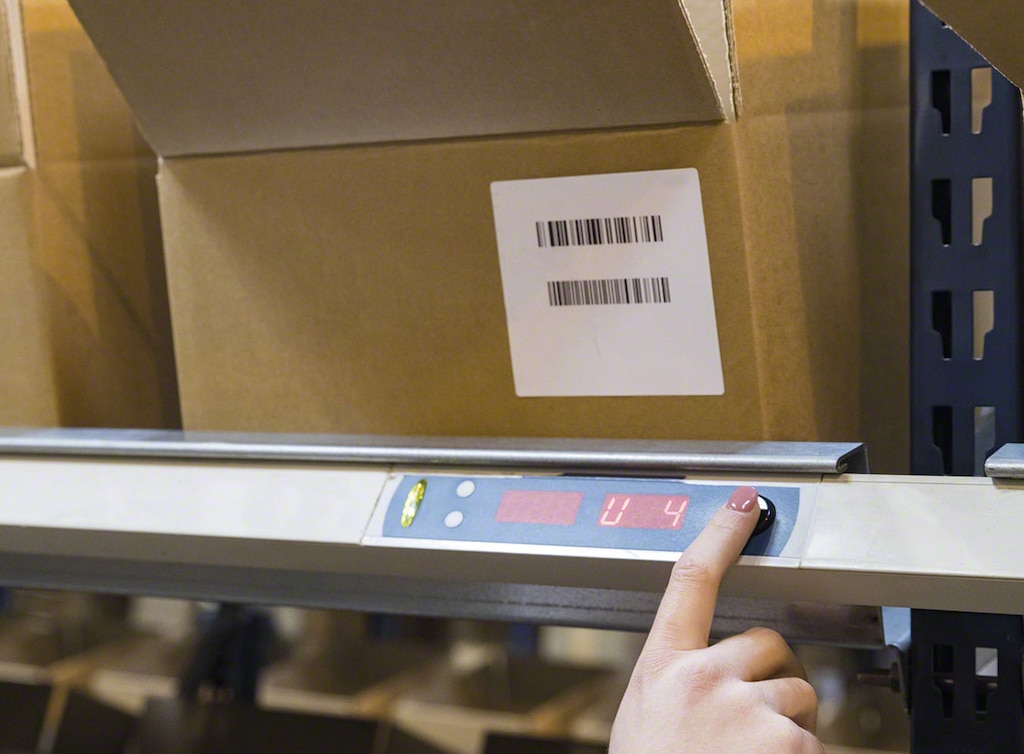
Esempio 3: Poka-Yoke raggruppato in cicli operativi di kitting
In molti magazzini si esegue il kitting, ossia un processo che riunisce le singole parti che costituiscono un prodotto creando un kit che altri operatori utilizzano per assemblare l’articolo finale.
Si tratta di un Poka-Yoke raggruppato, perché nelle postazioni di assemblaggio gli operatori hanno a disposizione tutti i materiali necessari per elaborare il prodotto e non devono percorrere il magazzino per localizzare i singoli componenti.
La preparazione anticipata dei kit garantisce rapidità e precisione. Si inizia a preparare un articolo riunendo i singoli componenti.
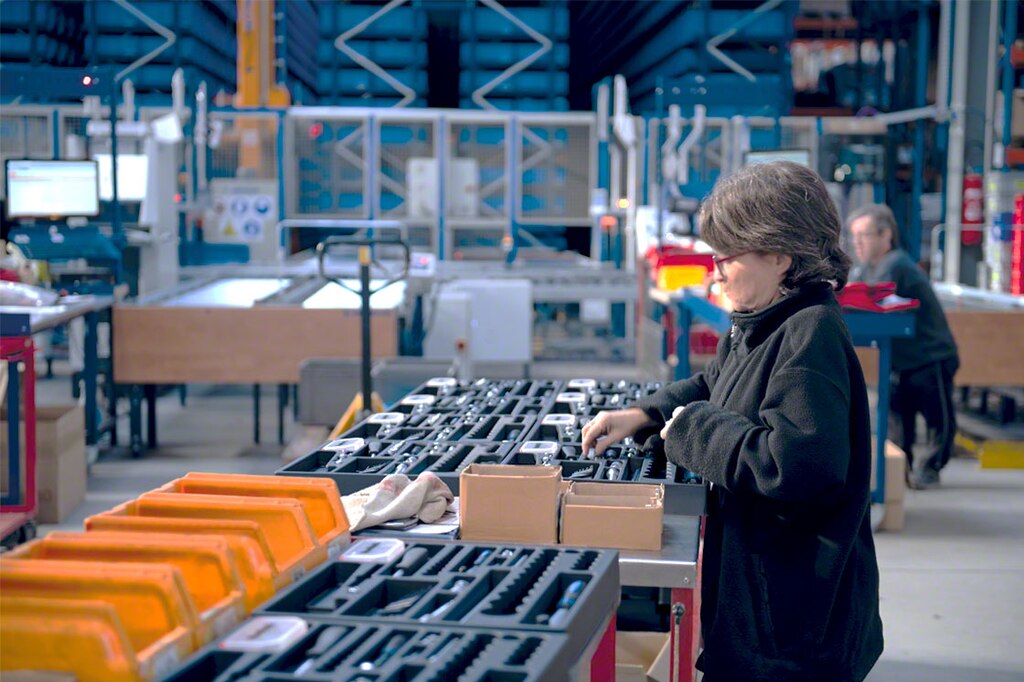
Esempio 4: Poka-Yoke fisico grazie alle chiusure di sicurezza
Il Poka-Yoke fisico più comune in un magazzino si basa sulle recinzioni di sicurezza. Più che prevenire gli errori, ha soprattutto la funzione di evitare incidenti.
Le aree in cui operano i mezzi di movimentazione automatici come i trasloelevatori sono protette per evitare l’accesso di personale non autorizzato. Quando una persona attraversa queste recinzioni e accede all’area di lavoro di un trasloelevatore - per svolgere attività di movimentazione o anche solo per errore - la macchina si ferma.
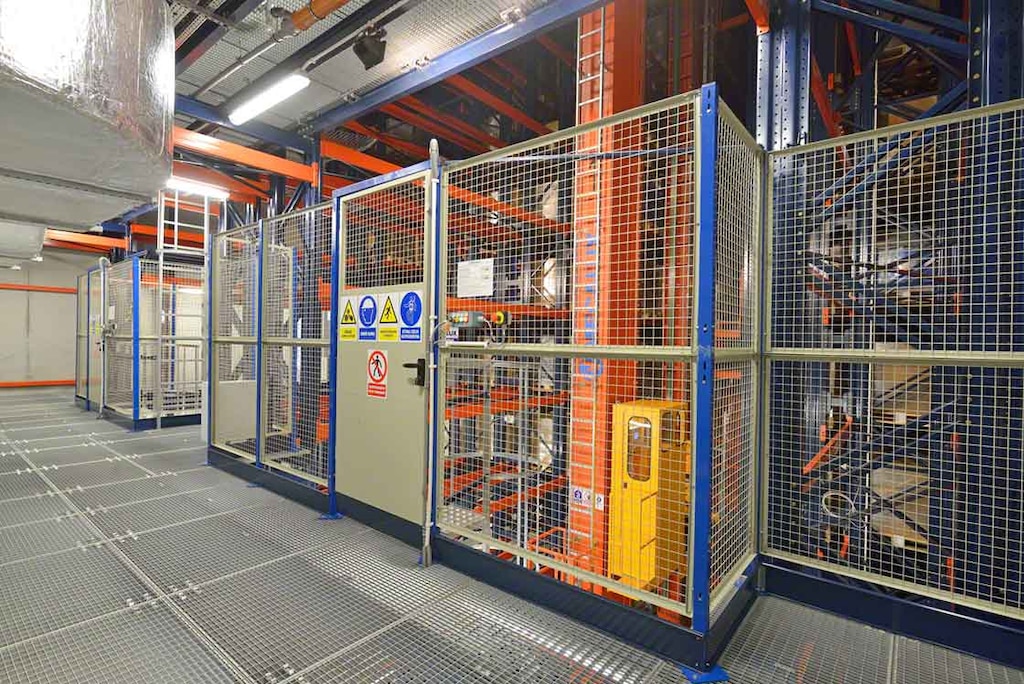
Esempio 5: Poka-Yoke fisico usando navette per picking
Un altro Poka-Yoke fisico comune nei magazzini è la navetta per la preparazione degli ordini. Di norma, ha dimensioni precise basate su quelle dei prodotti e degli ordini.
Se poi in un magazzino si effettua il picking a ondate o wave picking, le navette vengono suddivise su tante ubicazioni quanti sono gli ordini compresi nell’ondata. In questo modo, ogni ubicazione corrisponde a un ordine e si evitano errori.
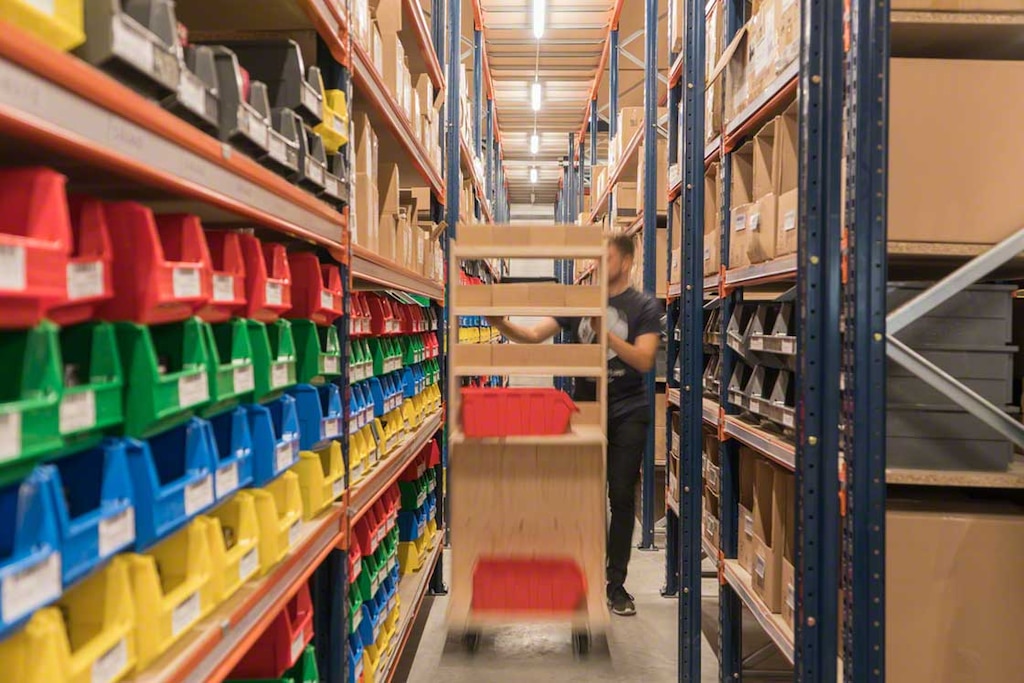
Eliminare errori, potenziare la qualità
Il Poka-Yoke applica tecniche che consentono di evitare errori, soprattutto nelle attività più ripetitive. Si è potuto constatare che appartiene alla nostra quotidianità, con oggetti e apparecchi di normale utilizzo nella vita oltre che nei magazzini e negli stabilimenti produttivi.
Il Poka-Yoke ha l’obiettivo di elevare la qualità dei processi e, di conseguenza, del servizio e del prodotto finale. In tal modo, aumenta anche la soddisfazione del cliente.
Mecalux vanta una vasta esperienza nello sviluppo di sistemi di stoccaggio che possono semplificare i cicli operativi del tuo magazzino e aumentare la produttività. Contattaci, progetteremo insieme a te un magazzino efficiente e pronto per evitare qualsiasi possibilità di errore.