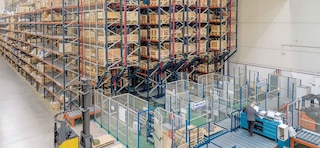
Lean Logistics: ridurre gli sprechi, creare valore aggiunto
Con l’espressione Lean Logistics (o Logistica Lean) si intende un tipo di filosofia o approccio relativo all’organizzazione operativa di un luogo di lavoro. Con questo termine di origine giapponese ci si riferisce all’insieme di metodi e logiche che permettono di identificare ed eliminare tutte le attività che non apportano valore, allo scopo di incrementare il flusso dei materiali - dai componenti al prodotto finito - per soddisfare la domanda del cliente finale.
Il concetto lean si può riassumere in una frase: “fare di più e meglio con meno” o, in altre parole, operare con meno sforzi, meno risorse, meno spazio, meno sprechi (e costi) e in meno tempo.
Inizialmente questo insieme di metodi, creati da Taiichi Ohno Toyota, vennero applicati nell'ambito della produzione automotive. Con il tempo però il concetto di lean non è rimasto circoscritto al lean manufacturing, ma è stato esteso ad altri campi d’applicazione.
Principi della metodologia Lean Logistics
La logistica lean ha come principale obiettivo ridurre i costi logistici concentrandosi sulle attività che non generano valore aggiunto a un processo. In tal modo verranno anche ridotti i tempi di ciclo. La ricerca costante dell’efficienza può essere suddivisa in varie fasi o principi:
1. Identificazione delle attività che aggiungono valore
Il primo passo consiste nello scomporre tutte le attività che compongono un intero processo. Grazie a strumenti come il Value Stream Map (o VSM, metodo di visualizzazione grafica utilizzato in ambito industriale al fine di individuare gli sprechi nei processi produttivi) è possibile individuare le inefficienze. Un caso chiaro sono le attività di picking organizzate in più fasi, dove ad ognuna di esse corrispondono diversi sottoprocessi, ciascuno dei quali può essere ottimizzato.
2. Individuazione degli sprechi e delle opportunità
Nella logistica gli sprechi sono spesso collegati alla perdita di tempo, argomento che vedremo più avanti. La standardizzazione delle attività logistiche e la manutenzione dei sistemi - includendo la pulizia del magazzino - sono essenziali in questo passaggio.
3. Creare un nuovo flusso di processi ottimizzato
Si tratta di progettare un nuovo metodo di lavoro più efficace in termini di tempo speso e qualità del servizio. Per fare ciò, le attività non necessarie devono essere identificate come sprechi ed eliminate.
Oltre ai cambi organizzativi, questa fase può comportare la necessità di realizzare investimenti in nuove tecnologie e sistemi che aiutino ad eliminare le fasi dei processi che non generano valore.
4. Strategia pull e minimizzazione dell’inventario
La quantità di scorte a magazzino incide sui costi di stoccaggio. A tal proposito, la logistica lean promuove l’abbandono di tecniche push (produzione basata sulle previsioni di vendita) in virtù di tecniche di tipo pull (si produce rispondendo alla domanda in maniera agile).
5. Standardizzazione dei nuovi processi e mantenimento
Per fare ciò, è indispensabile coinvolgere e motivare tutti i lavoratori, fornendo loro una formazione adeguata. In tal modo possono acquisire nuove abitudini e le competenze che caratterizzano il talento 4.0.
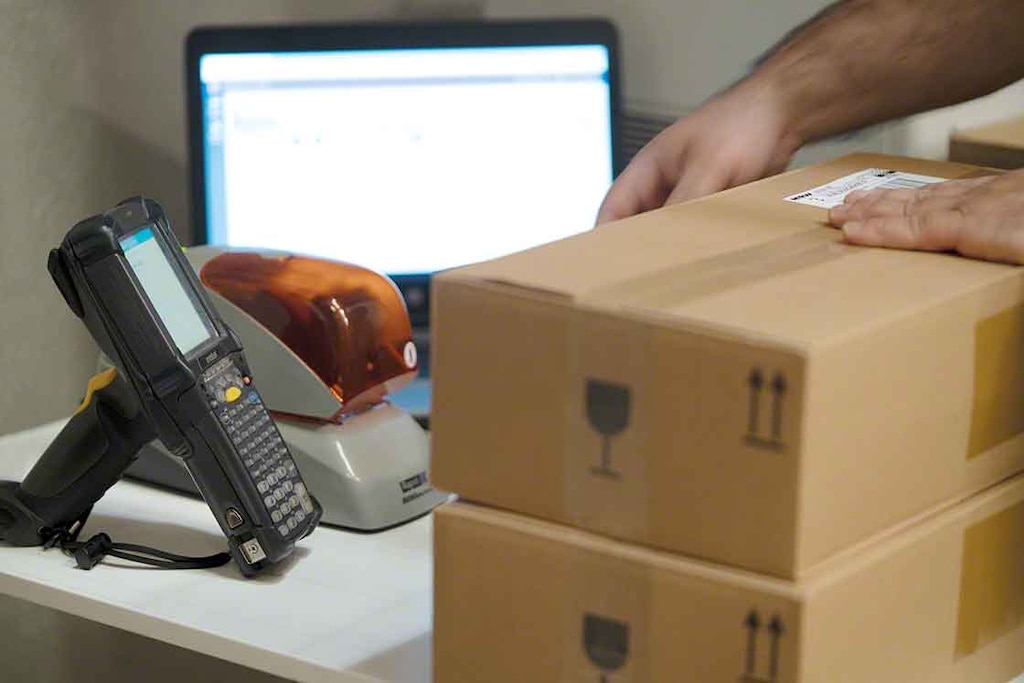
Principali sprechi eliminabili con il metodo lean
È possibile classificare gli sprechi in quattro grandi gruppi. Vediamo nel dettaglio quali sono e come possono essere trattati con la logica lean.
- Eccesso di stock
Le cause principali che creano questo problema sono gli eccessi di produzione nelle imprese manifatturiere, ma anche una errata previsione della domanda (demand forecasting).
Lo stock in eccesso è frutto anche della volontà delle imprese di volersi esageratamente tutelare, producendo più scorte di sicurezza del dovuto. In questi casi bisognerebbe intervenire sul problema reale, che spesso si cela in una gestione poco efficiente dei fornitori o dei flussi di materiali.
L'importanza di questo punto è palpabile in quanto gli sprechi riguardano sia l'utilizzazione delle spazio, sia i costi di stoccaggio (in quanto si producono dei costi legati a delle scorte a bassa rotazione che praticamente non si muovono mai).
Come risolvere questo problema con la logica della logistica lean
L’approccio lean suggerirebbe innanzitutto di agire su tutti i fattori controllabili, lasciando per da parte per un momento più complessi da verificare (la previsione della domanda, ad esempio). Con questa premessa, è possibile delineare una serie di strategie lean utili per ridurre l’eccesso di stock:
- La tecnica del cross docking, utile per prescindere dei sistemi di stoccaggio o per lo meno ridurli al minimo.
- Il modello gestionale del just in time (o JIT), per una gestione virtuosa dei fornitori e dello stock a magazzino.
- La riduzione del lead time relativo ai fornitori e ai processi intralogistici. Questo faciliterà il calcolo della previsione della domanda, che sarà più precisa in quanto gli intervalli di tempo sono più vicini (fattore che limiterà le incongruenze e l’inventario in eccesso).
- Tempi di attesa e colli di bottiglia
Le cause che fanno sorgere questi problemi possono essere molteplici, ma quasi tutte sono ricollegabili a un metodo di lavoro pianificato male o all’assenza di equilibrio nella distribuzione delle attività di lavoro tra gli operatori del magazzino.
La logistica lean, oltre a distribuire in maniera equilibrata le task, punta con i suoi metodi a standardizzare i tempi di lavoro: in questo modo a ogni attività o azione corrisponde un preciso tempo di esecuzione. Il tempo di esecuzione del lavoro è quello per cui paghi gli operatori di magazzino, mentre il tempo standard è quello che paga il cliente. Quando ogni tempo è predeterminato, si riducono le inefficienze, si migliora il servizio e, soprattutto, si risparmia.
Come eliminare le attese e i colli di bottiglia grazie all’approccio lean
- Per organizzare le attività nel magazzino ed evitare sia i colli di bottiglia sia i tempi morti, non esiste strumento migliore del software per la gestione del magazzino. Grazie al software è possibile gestire una notevole quantità di informazioni e organizzare i dati al fine di ottimizzare i processi.
- Analizzare e controllare il carico di lavoro di ogni operatore per evitare disequilibri. Il software di magazzino dispone di un modulo per misurare il rendimento dei dipendenti.
- Realizzare la manutenzione preventiva dei sistemi di stoccaggio automatico e dei mezzi di movimentazione: questa misura permette di evitare avarie che potrebbero sfociare in uno stop alle attività di magazzino.
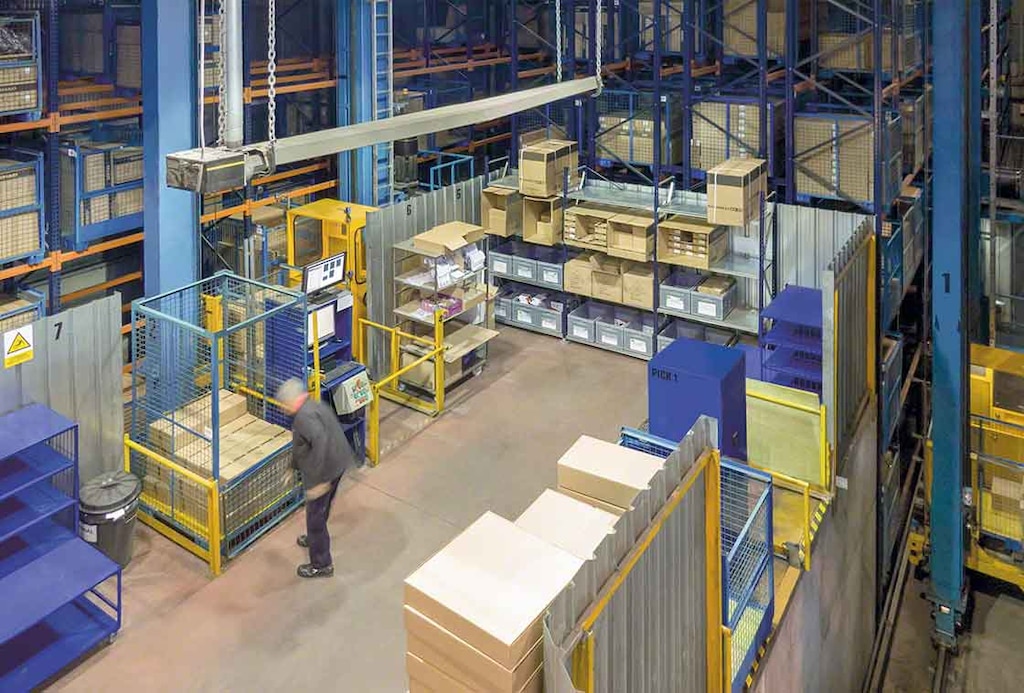
- Spostamenti e movimenti inutili
Le attività di picking e preparazione ordini devono essere adeguatamente pianificate in quanto sono operazioni che occupano una grande quantità di tempo e risorse. Una pianificazione inadeguata delle linee e dei percorsi di picking potrebbe invece generare inefficienze (viaggi a vuoto verso gli scaffali, ad esempio), che a loro volta ricadrebbero (negativamente) sulla produttività del centro.
Come risolvere le inefficienze legate alla movimentazione grazie all’approccio lean
- L’automazione della movimentazione dei carichi è un'ottima strategia per ridurre il tempo dedicato alle attività di trasporto interne e al contempo aumentare la sicurezza operativa. Quando gli spostamenti sono ripetitivi, conviene optare per sistemi automatici che permettono di guadagnare tempo e di standardizzare al massimo i tempi. Nel caso dei trasloelevatori, ad esempio, è possibile ottimizzare i tempi al massimo in quanto questi robot sono in grado di lavorare con cicli combinati.
- Le strategie di picking ed evasione degli ordini possono essere supportate in termini organizzativi mediante l’implementazione di un software di magazzino. Il programma permette di organizzare meglio i percorsi di picking all’interno del centro, tenendo in considerazione il consolidamento delle merci o le necessità di invii speciali, quali ad esempio le spedizioni realizzate con la tecnica del groupage.
- Errori che generano resi e ripetizione di interi processi
In generale, un livello più elevato di qualità è generalmente associato a costi più elevati, ma non è sempre così. Le migliori aziende del settore logistico, molte delle quali hanno una logistica lean, si caratterizzano per offrire un servizio eccellente al giusto prezzo. Questo avviene principalmente perché la loro logistica è pressoché infallibile (quindi non devono ripetere due volte lo stesso processo).
Come ridurre i resi grazie alla filosofia lean
- Quando la reverse logistics (logistica inversa) complica le operazioni del magazzino, conviene fermarsi ed analizzare le cause che portano a tale situazione. Se alla base del problema si trovano degli errori nella fase di preparazione ordini, allora è possibile ricorrere a software e moduli specifici.
- Identificare le incidenze in tempo è una buona maniera per evitare di realizzare due volte le stesse attività e processi.
La metodologia lean logistics: focus sul risparmio
Il concetto di logistica lean parte dalle premessa che il cliente, quando compra un prodotto, non è cosciente né paga gli sprechi generati lungo l’intera supply chain. Per questa ragione, l’approccio
Mecalux dispone di una vasta gamma di soluzioni di stoccaggio tradizionali, automatiche e 4.0 in grado di migliorare l’efficienza del tuo centro. Contattaci e un nostro esperto ti aiuterà a scegliere le soluzioni di stoccaggio migliori per il magazzino efficiente.