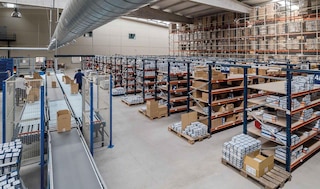
Attività di picking e organizzazione del lavoro
Le attività di picking o di preparazione degli ordini sono fasi operative complesse e costose per le imprese. In primo luogo perché impegnano tutte le risorse presenti in un magazzino: personale, mezzi e spazio. In secondo luogo perché i cicli di picking vanno a impattare direttamente sul livello di servizio e sulla soddisfazione dei clienti.
Gli scenari di mercato attuali, poi, contribuiscono a rendere la sfida ancor più delicata. Alla già alta intensità di lavoro dei magazzini in cui il picking si svolge manualmente, si aggiungono l'aumento dei codici da gestire, liste di prelievo più lunghe e lead time ridotti. Viste queste premesse, si comprende perché per le aziende è fondamentale organizzare al meglio il workflow delle attività di picking per restare competitive.
Per farlo, è necessario prima "scomporre" il processo di order fulfillment e schematizzarne i passaggi. In questo articolo ci occupiamo proprio di questo: analizziamo le diverse fasi dell'attività di picking per capire dove agire per essere più produttivi.
Fase 1: Pianificazione
La pianificazione è il passo che precede l'attività vera e propria di picking. In questa fase ha luogo l'organizzazione dei prelievi e si distribuiscono le liste di prelievo. Esattamente come avviene nel caso del ricevimento merci, una buona pianificazione delle attività di picking deve tenere conto delle caratteristiche del magazzino e delle risorse presenti al suo interno: la superficie disponibile, la distribuzione delle aree del magazzino, i sistemi di stoccaggio, la disposizione delle scaffalature per picking o le condizioni di luce.
Analogamente, contempla i fattori quali le skill del personale, la tipologia delle task da svolgere o il tipo di mezzi impiegati per la movimentazione dei materiali.
La profonda conoscenza di questi aspetti permette, ad esempio, di fissare dei "tetti" per le liste di prelievo, ovvero un numero massimo di ordine che ogni picker può gestire (definiti per garantire la giusta velocità di esecuzione delle attività) e di stabilire la turnazione degli addetti alle aree di picking. Vista l'importanza di programmare ogni movimento nei minimi dettagli, le aziende sfruttano sistemi informatici WMS che contribuiscono a migliorare sensibilmente la pianificazione delle attività picking.
Fase 2: Percorsi e politiche di routing
Quando il prelievo avviene con il criterio "uomo alla merce", le percorrenze vanno a incidere direttamente sull'efficienza operativa. Per questa ragione bisogna ottimizzare i percorsi e ridurre al minimo i tempi di spostamento. In un magazzino un percorso non è una semplice "linea" retta da accorciare, ma è la somma di questi tre segmenti:
- La distanza dal punto di partenza fino allo scaffale sul quale si trova ubicato il primo prodotto.
- Dall'ubicazione del primo prodotto al seguente.
- Il percorso di ritorno fino alla zona di approntamento e spedizione.
Come ridurre le distanze ed evitare percorsi a vuoto.
Una soluzione "a costo zero” è avvicinare all’operatore le referenze che presentano un indice di rotazione elevato, in maniera da ridurre i tempi di percorrenza e i cicli di sollevamento dei carrellisti. Esistono poi una serie opportunità di miglioramento che sono legate al layout di magazzino e ai mezzi di movimentazione.
Per quanto riguarda il layout, dove possibile, è meglio eliminare gli ostacoli strutturali che intralciano le attività di picking. Per quel che concerne i mezzi di movimentazione, è auspicabile operare un confronto tra il rendimento dei carrelli e delle soluzioni di picking automatico in quanto possono sostituire i carrelli elevatori.
Fase 3: Prelievo
Seppur possa apparire scontato, vale la pena ricordare che i tempi di prelievo di un prodotto stoccato in scaffalature a grandi altezze sono più lunghi rispetto a uno che è si trova "a terra". Nei tempi di presa va incluso l'intervallo che si impiega per raggiungere l'altezza dello scaffale e, trattandosi di un prelievo più rischioso, non bisogna mai ottimizzare a discapito delle procedure di sicurezza.
Un attività di prelievo senza complicazioni
Per prelevare gli articoli in maniera efficiente è necessario:
- Un controllo esaustivo dell'inventario che rifletta fedelmente la quantità di merci presenti all'interno dell'impianto.
- Realizzare una mappatura smart e funzionale delle ubicazioni.
- È bene esplorare la possibilità di implementazione di sistemi quali voice-picking, pick-to-light o put-to-light.
- La manutenzione dei mezzi deve essere svolta regolarmente.
- Se il prelievo viene realizzato in altezza, conviene valutare l'installazione di trasloelevatori o di soluzioni automatiche pensate per ottimizzare i tempi legati a queste operazioni.
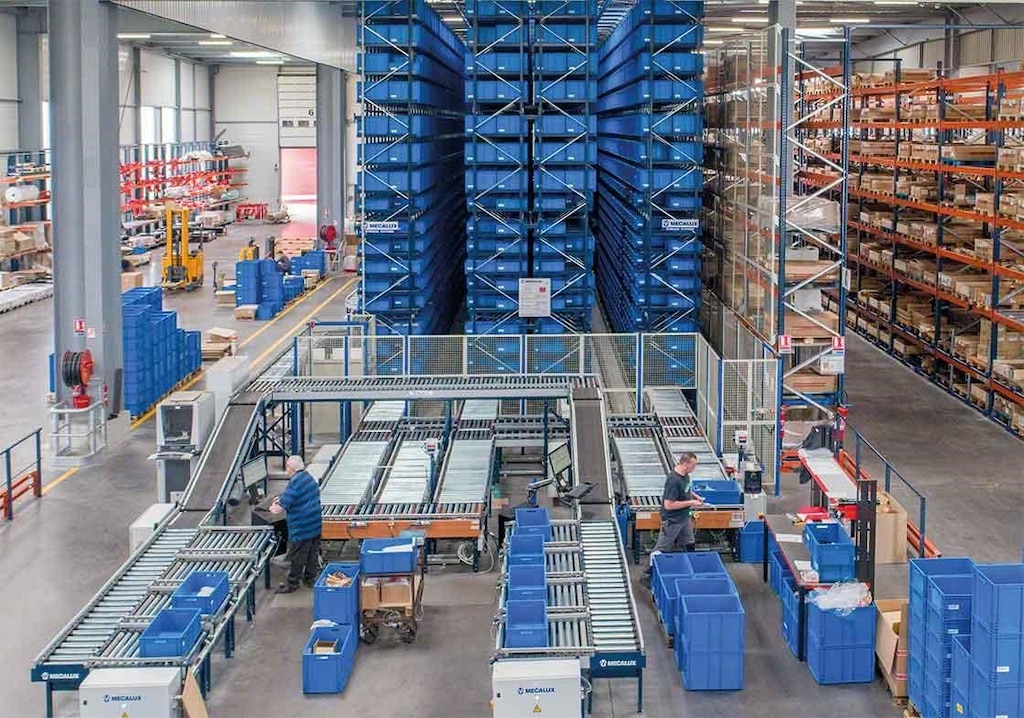
Fase 4: Controllo e allestimento degli ordini
Questa attività chiude il ciclo di picking e comprende:
- Controllo dei colli prelevati: si verifica che referenze e quantità siano quelle corrette.
- Approntamento degli ordini: pesatura, imballaggio ed etichettatura.
- Trasferimento dei colli all'area di smistamento in cui verranno suddivisi in funzione della modalità di consegna.
- Stampa della packing list, ovvero la bolla di spedizione per i trasportatori.
Come migliorare le fasi di approntamento della spedizione
Questa fase dell'attività di picking si può migliorare in due modi:
- Scegliendo gli imballaggi che consentono di guadagnare velocità e, al contempo, fornendo agli operatori gli strumenti adeguati per svolgere il loro lavoro in maniera efficace.
- Avvicinando lo stock agli strumenti per il packing.
- Seguendo gli stessi standard delle agenzie di trasporto logistico per l'etichettatura degli ordini e per la preparazione delle packing list.
- Fissando delle procedure chiare che sviluppino una certa ripetibilità delle operazioni. In questo modo si gli operatori svilupperanno degli automatismi che eviteranno dubbi inutili e rallentamenti nell'esecuzione delle task.
Order fulfillment accurato
L'accuratezza del processo di order fulfillment dipende dall'efficienza delle attività di picking: abbiamo visto però che il picking a sua volta è una fase operativa composta da diversi elementi da ottimizzare individualmente. Soltanto una combinazione di flussi documentali e di attività calibrati al millesimo garantisce un livello di servizio eccellente e un lead time competitivo.
Per alcuni magazzini, gli approcci che si basano su un'analisi dei processi basteranno a rendere migliore la performance operativa. In altri centri ciò non basta, e si può migliorare solo grazie ad avanzate soluzioni ingegneristiche. Mecalux, da più di 50 anni, si dedica a individuare le opportunità e far crescere le aziende grazie a soluzioni di stoccaggio che spaziano dalle solide scaffalature metalliche fino ai moderni magazzini automatici con integrati i sistemi WMS.
Per saperne di più su come velocizzare il ciclo di picking e migliorare il lead time, contattaci senza impegno.