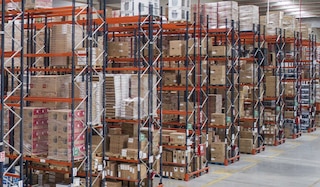
I 10 problemi logistici più comuni in magazzino
La costante evoluzione verso i mercati digitali e le nuove esigenze dei clienti hanno comportato un notevole aumento dei problemi logistici, soprattutto di quelli relativi alla gestione del magazzino.
Ma quali sono i problemi logistici più comuni? Identifichiamo i dieci che normalmente si verificano in un magazzino e suggeriamo alcune soluzioni per ridurre al minimo l’impatto.
1. Spazio inutilizzato
La mancanza di spazio di stoccaggio è uno dei principali problemi a cui deve far fronte la maggior parte delle aziende. Davanti a una situazione del genere, causata soprattutto da un aumento dell’attività, le aziende hanno l’obbligo di ottimizzare lo spazio se non vogliono affrontare un consistente esborso economico per lo spazio logistico.
Una soluzione spesso utilizzata per aumentare lo spazio senza alterare la superficie prevede di sfruttare l’altezza del magazzino utilizzando scaffalature più alte oppure soppalchi e passerelle. È inoltre possibile ottimizzare la superficie montando sistemi di stoccaggio intensivo, come i Pallet Shuttle, le scaffalature Movirack o le scaffalature drive-in.
2. Mancanza di organizzazione della merce
La mancanza di organizzazione della merce causa errori e ritardi quando si cerca un determinato prodotto, compromettendo il rispetto dei termini di consegna. Un magazzino ordinato è il primo passo verso l’efficienza logistica.
In quest’ottica, è necessario elaborare un’efficiente strategia di ubicazione della merce che tenga conto delle caratteristiche delle referenze, dei sistemi di stoccaggio disponibili, della rotazione della merce e degli spostamenti degli operatori.
L’uso di un software di gestione magazzino garantisce il controllo dell’intero stock presente in magazzino sincronizzando gli ordini in entrata e in uscita. Un WMS, ad esempio, automatizza il processo di ubicazione delle referenze in magazzino (slotting) in base a regole e criteri predefiniti.
3. Errori nel picking
Dal prelevare un articolo sbagliato alla mescolanza di più ordini: il costo della logistica inversa - i resi della merce - a causa di errori nel picking ha sempre gravi conseguenze sulla logistica aziendale.
Gli errori nel picking comportano un costo elevato per il business.
Alcuni studi stimano che l’impatto medio sia di 17 € a ordine.
In un ciclo operativo complesso come la preparazione degli ordini, dove in genere gli operatori elaborano più ordini di referenze diverse, l’automazione è la soluzione per ridurre la percentuale di errori e aumentare il numero di picking completati ogni ora in magazzino.
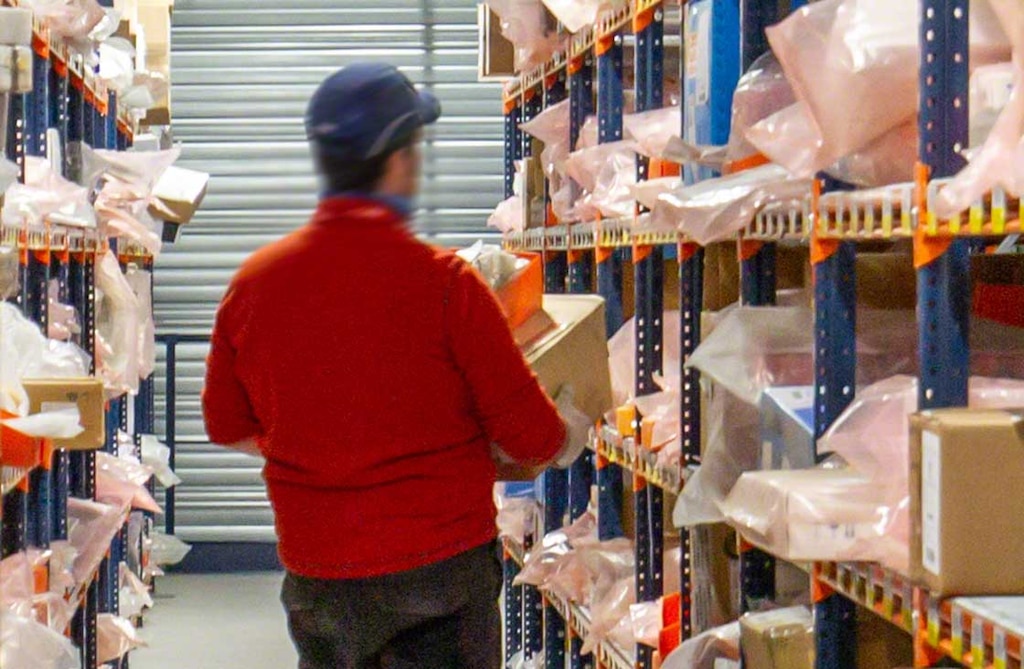
4. Mancanza di tracciabilità
All’interno di una supply chain integrata, clienti e fornitori vogliono sapere con quali materie prime è stato prodotto un articolo e quali processi produttivi e logistici ha attraversato prima di arrivare nelle loro mani.
La tracciabilità del prodotto, l’attributo logistico che consente di registrare e identificare un articolo dall’origine alla destinazione finale, assume un ruolo particolarmente delicato in settori come quello farmaceutico o agroalimentare . Un errore di tracciabilità può comportare gravi problemi per i clienti che acquistano il prodotto e per il fornitore.
L’implementazione di un software logistico come un WMS garantisce la tracciabilità del prodotto dall’entrata in magazzino alla spedizione. Come integrazione di questa applicazione, sul mercato sono disponibili altri programmi software che potenziano l’aspetto logistico come, ad esempio, la funzionalità avanzata di Easy WMS, WMS per la produzione. Il modulo, infatti, sincronizza il polmone di approvvigionamento con quello di produzione al fine di monitorare il processo produttivo in magazzino.
5. Inventario obsoleto
Conoscere e pianificare lo stock di un magazzino è indispensabile per garantire la produttività in tutte le operazioni logistiche. Non a caso, un magazzino con un inventario obsoleto può implicare gravi conseguenze per un’azienda: dagli errori nell’ubicazione dei prodotti a un’eventuale rottura di stock.
Quando un’azienda comincia a svilupparsi e ad acquisire sempre più referenze, l’implementazione di un software di gestione magazzini diventa una scelta necessaria per essere sempre informati sulla disponibilità dello stock in magazzino.
6. Errori nella movimentazione della merce
La corretta movimentazione delle unità di carico per la preparazione degli ordini rappresenta uno dei segreti per ridurre gli errori e aumentare la produttività. Bisogna far sì che gli operatori siano opportunamente addestrati e il magazzino sia dotato di idonei mezzi di sollevamento sottoposti a debita manutenzione.
Tuttavia, l’opzione che più garantisce la corretta movimentazione della merce è l’automazione dei sistemi di stoccaggio. I responsabili della logistica scelgono di sostituire i mezzi di movimentazione tradizionali come transpallet e carrelli controbilanciati, con trasportatori e trasloelevatori, con l’obiettivo di rendere più dinamico il transito della merce tra i vari processi logistici.
Inoltre, durante la movimentazione della merce, è importante che le unità di carico, in genere pallet o contenitori, siano ben saldi per garantire la stabilità dei colli durante tutti i cicli operativi svolti in magazzino.
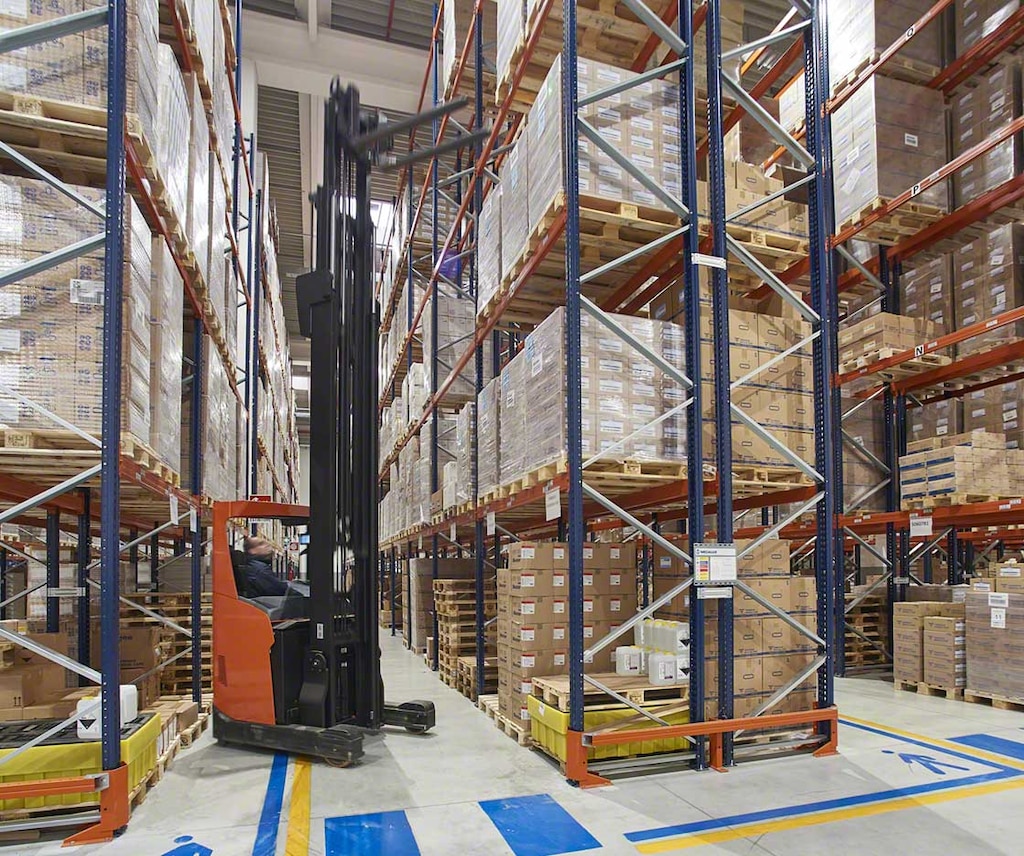
7. Ritardi nelle spedizioni
La spedizione della merce è l’ultimo processo che un prodotto attraversa prima di essere inviato al cliente finale o a un altro centro di distribuzione o produzione.
Per completare il processo con successo, è consigliabile implementare una pianificazione delle consegne, un efficace consolidamento della merce, una corretta verifica di tutta la documentazione necessaria per la spedizione e un caricamento rapido e sicuro della merce sui camion.
Un software di gestione magazzini è in grado di raggruppare gli ordini, ad esempio per percorso di consegne, tipo di veicolo, cliente o priorità di spedizione.
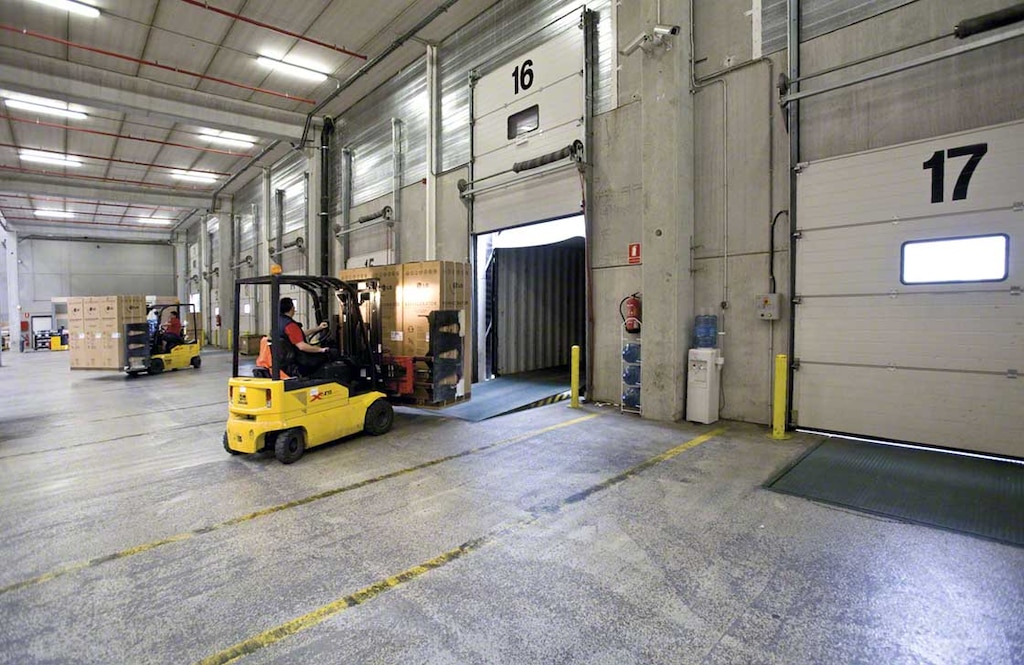
8. Segnaletica insufficiente nel magazzino
In uno spazio in cui convivono operatori e merce, la segnaletica in magazzino è obbligatoria al fine di ridurre al minimo il rischio di incidenti. I segnali devono essere correttamente posizionati e visivamente differenziati sul pavimento e sulle scaffalature in ottemperanza alle misure di sicurezza.
Le caratteristiche dei segnali sono oggetto della Direttiva 92/58/CEE del Consiglio europeo, che impone e disciplina la segnaletica nei magazzini. I colori, i simboli e la forma dei segnali variano a seconda della funzione e del messaggio che comunicano.
9. KPI della logistica sbagliati
Gli indicatori di performance o KPI della logistica (Key Performance Indicator) sono lo strumento migliore per implementare azioni di miglioramento continuo nel magazzino. Analizzando i dati e confrontandoli con lo storico dell’azienda, è possibile monitorare la performance di un ciclo operativo con l’obiettivo di trovare opportunità di miglioramento.
I KPI della logistica misurano i cicli operativi che si svolgono in magazzino, tra cui: ricevimento della merce, stoccaggio, preparazione degli ordini, gestione dell’inventario, spedizioni, consegne, trasporto e gestione dei resi. Se non utilizzati correttamente o se si analizzano i KPI sbagliati, sarà molto difficile rilevare evoluzioni positive o negative e agire di conseguenza per raggiungere l’eccellenza logistica.
Un modulo come Supply Chain Business Intelligence monitora ogni attività del magazzino calcolando i KPI della logistica più importanti per l’analisi successiva.
10. Integrazione con gli altri reparti (ERP)
Il responsabile del magazzino si deve coordinare con gli altri reparti dell’azienda per raggiungere l’obiettivo finale di tutta la logistica: la consegna degli ordini nei termini e secondo le modalità concordate con il cliente.
A tal fine, i vari programmi software si integrano nell’applicazione ERP (Enterprise Resourcing Planning), un programma che riunisce tutti, o almeno in maggioranza, i reparti di un’azienda come, ad esempio, contabilità, marketing, ufficio commerciale ecc.
Un coordinamento improprio tra magazzino e reparto vendite può causare ordini sbagliati o incompleti, con gravi conseguenze economiche per l’azienda.
Sfrutta i vantaggi di un magazzino più efficiente
In generale, l’automazione dei cicli operativi e della gestione di un magazzino mediante un WMS è la strategia migliore per ottenere un magazzino senza errori e molto più efficiente.
Se il tuo magazzino presenta uno dei problemi discussi sopra oppure pensi che sia arrivato il momento di robotizzare lo stoccaggio e la gestione del tuo centro di distribuzione, non esitare a contattare Mecalux. Un team di esperti ti aiuterà a superare ogni ostacolo per sfruttare al meglio i tuoi processi logistici.